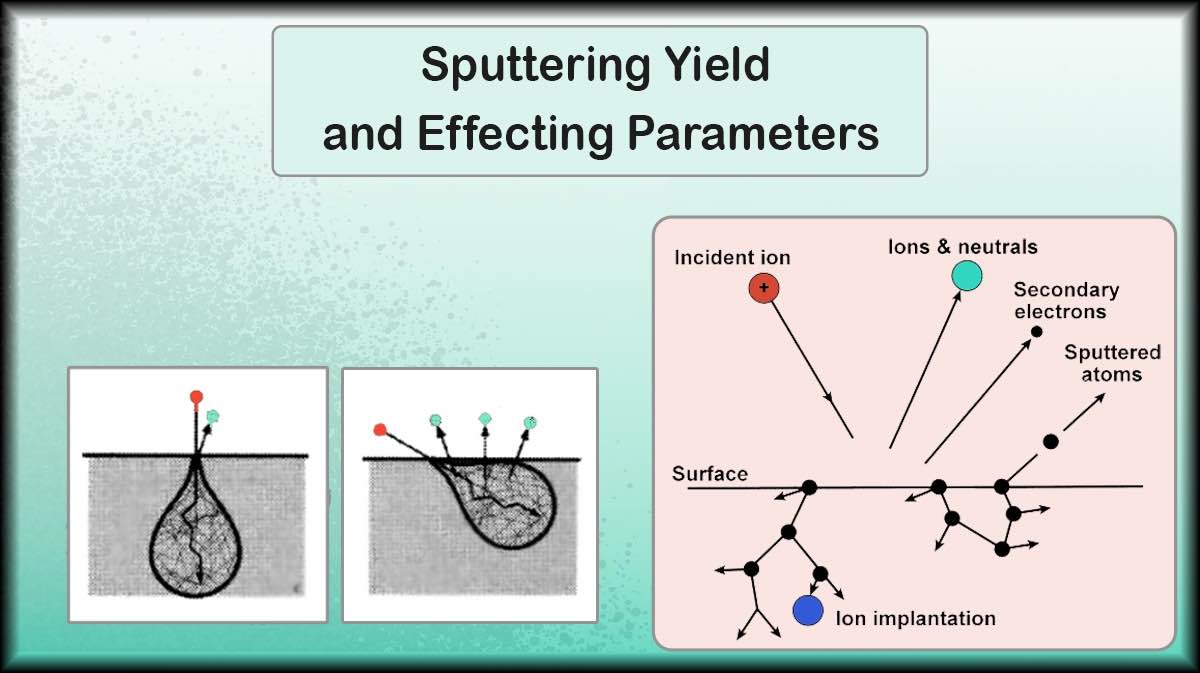
Sputtering Yield
Sputtering is caused by energetic ions bombarding a source material as the target in a plasma. The ratio of the ejected atoms from the target per incident plasma ion is known as the sputter yield. The sputter yield depends on several parameters in relation to the sputtering chamber, such as pressure, or the target material composition, and is a key factor in the sputter coating process.
What is the Sputtering Yield?
Deposition of thin films of different materials by DC or RF sputtering is a known coating method widely used in the deposition of hard coatings, thin film semiconductors, solar cell fabrication, SEM sample preparation, etc. The sputtering coating efficiency is highly dependent on the sputter yield of the target material, the ratio of atoms removed from the target surface per incident energetic ions from the plasma, and subsequently deposited on the substrate.

The sputtering yield S is formulated as the average number of atoms removed from the surface of the target per incident ion:
S = (number of atoms removed)/(number of incident ions)
Sputter Yield or Sputter Rate?
The sputtering rate is usually referred to as the sputter yield multiplied by the ion current to the target. Therefore, these two concept are commonly used interchangeably, as we will do in this article afterward.
What Factors Affect the Sputter Yield?
The sputter yield is affected by the following factors:
- Energy of incident ions
- Sputter gas pressure
- Target material composition
- Incident angle of ions
- Crystal structure of the target surface
Incident Ion Energy Effect On The Sputtering Yield
The sputtering yield as a function of ion energy is shown in Figure 2. At very low energies, incident ions cannot remove atoms from the target surface, hence there is no sputtering yield. The sputtering process begins at the threshold energy, which could be up to 40 eV for most materials, and is very sensitive to contamination of the cathode surface, the incident angle of ions, and the crystal orientation of the target material.
In the knock-on sputtering regime, the sputter yield has a linear dependence on the incident ion energy (In a log-log curve).

In the cascade region the incident ions cause a cascade of target atoms, whose bonds are broken within a cascade volume.
At higher ion energies, the ions penetrate deep into the target materials and implant there, lowering the sputtering rate.
Sputter Process Gas Pressure
Lowering the sputter gas pressure in RF or DC sputtering process in the power control mode results in a slight increase in the plasma-to-target voltage. Consequently, the ions bombarding the target will gain higher energies that enhances the sputter yield and so the sputter rate.
Target Material Composition
The sputtering rate of compound targets is different from their component elements. In a research at the National Institute for Materials Science in Japan, the measurement of the sputtering yields of pure elements, like Co, Cu, Ni, Ti, and their silicides (Nickel, cobalt, and titanium silicides) represents that the sputter yield of the silicides could be estimated by the linear combination of the sputter yields of the component elements.
The Incident Angle of Ions
Sputter yield dependence on the angle of ion incidence is stronger for materials with lower sputter yield (e.g., Ta, Mo, Fe) compared to material with higher sputter yield (e.g., Au, Ag, Cu).

Sputter Yield Measurement
The sputtering rate calculation can be done by several methods. Some of the methods for sputter rate measurement include:
- Measuring the weight loss of the target by utilizing a Quartz Crystal Microbalance (QCM) sensor to detect slight changes in the target mass
- Measuring the decrease of the target thickness by surface analysis techniques like SEM to measure minute changes in the target thickness
- Determination of changes in the surface composition by RBS during the sputtering process with an accuracy of about 10%
- Collection of the sputtered materials
- Detection of sputtered particles in flight
Sputtering Yield Amplification
For targets made of light elements like carbon, the momentum transfer is low and the collision cascade may spread into the target bulk, so sputtering is not very effective. In these cases, the atom-assisted sputtering yield amplification technique is practical. In this method, the sputter yield increases by amplifying the collision cascade when reflected by the heavier atoms implanted a few monolayers beneath the target surface. A carbon target with embedded Pt atoms shows an increase in sputter yield by a factor of 3.

How Magnetron Cathodes Enhance Sputter Rate?
The sputtering rates can be significantly improved using magnetron cathodes, so the magnetic field of cathode magnets behind the target will trap the charged particles of the plasma in helical paths close to the target. This excessive concentration of electrons in the near-target region results in higher ionization rates, so enhanced sputter rate at a lower process pressure.
Sputtering rates scale linearly by the number of magnets. Therefore, once the desired sputter rate is not achievable by maximizing the sputtering power, increasing the number of magnets can be helpful.
Vac Coat Sputter Coaters and Sputtering Rate
The sputtering rate or sputter yield is a key factor in an efficient sputter coating process and depends on various parameters, such as target material composition and structure, incident ion energy and angle of incidence. The sputtering yield of a target can be amplified through various methods like implanting a monolayer of heavy atoms below the target surface. The sputter rate can be also adjusted utilizing magnetron cathodes.
All Vac Coat sputter coating systems, like single cathode sputter coaters DSR1, DST1, or multi-cathode high vacuum sputter coaters DST3 or DST2-TG, are supplied with magnetron cathodes to enhance the sputtering rate of different targets.
Some of Vac Coat Systems
References
- Wasa, Kiyotaka. “Sputtering phenomena.” Handbook of Sputtering Technology (2012): 41-75.
- Bräuer, G. “Magnetron sputtering.” (2014).
- Sarkar, Jaydeep. “Sputtering and thin film deposition.” Sputtering Materials for VLSI and Thin Film Devices; Elsevier: Amsterdam, The Netherlands 2 (2014): 93-170.
- Yoshitake, Michiko, Yasuhiro Yamauchi, and Chandra Bose. “Sputtering rate measurements of some transition metal silicides and comparison with those of the elements.” Surface and Interface Analysis: An International Journal devoted to the development and application of techniques for the analysis of surfaces, interfaces and thin films 36.8 (2004): 801-804.
Dawber, M. “Sputtering techniques for epitaxial growth of complex oxides.” Epitaxial Growth of Complex Metal Oxides. Woodhead Publishing, 2015. 37-51.
- https://www.lesker.com/leskertech/archives/0g11m3h/leskertech_v7_i1.pdf