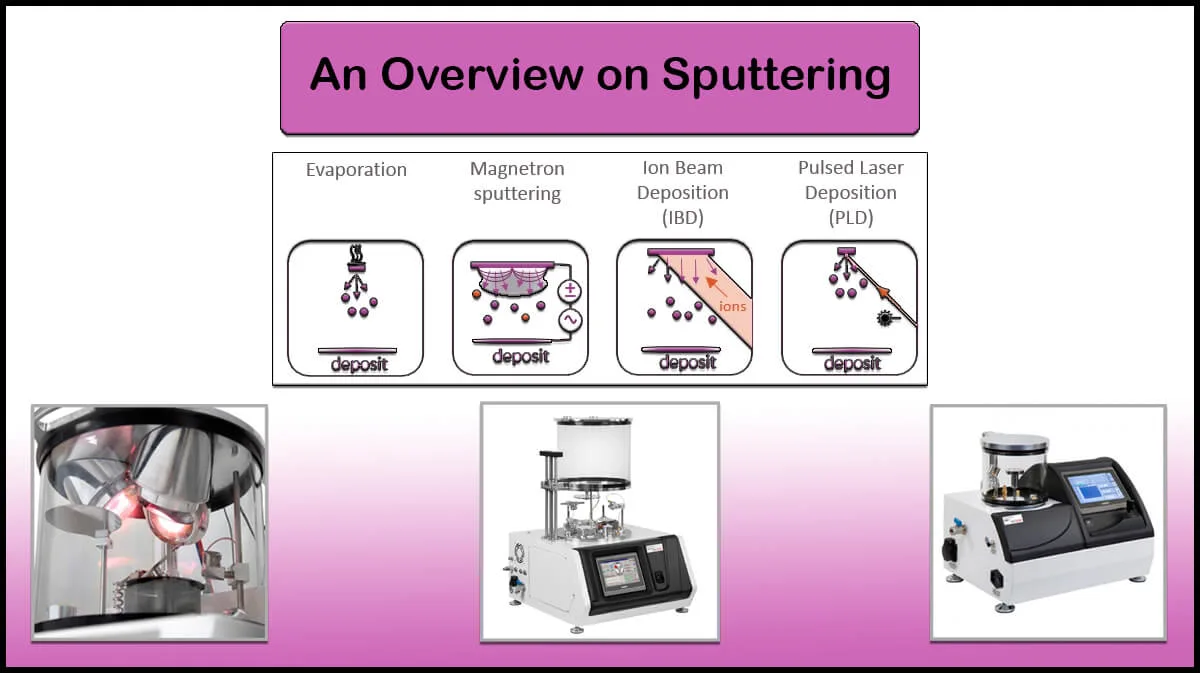
An Overview of Sputtering
Sputtering in physics is called to the process in which a plasma of high energy particles/ions knock out the species on the surface layer of a solid target. This phenomenon naturally happens in the outer space, constantly forming the universe and causes spacecraft’s corrosion. Here, on Earth, the science and industry make use of sputtering process to generate or eradicate thin films of nano/micrometer thickness for various applications in optics, electronics, etc.
What is Sputtering?
Due to the collision of high-energy ions with the target material atoms, momentum transfer occurs between them. These ions, called incident ions, cause a series of collision cascades on the surface of the target. Sometimes these successive collisions cause the ions to travel long distances and lose their energy. If the ion energy at the time of reaching the target surface is greater than the bonding energy between the atoms of the target material, the collided atom separates from the target material. This phenomenon is called Sputtering.
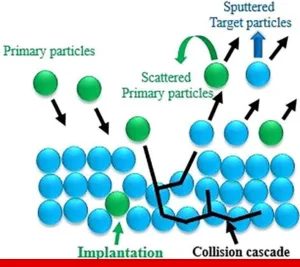
Sputter Yield
The energy of sputtered atoms varies widely, and usually the kinetic energy of these atoms is more than tens of electron volts (typically 600 eV). Approximately one percent of the ions that hit the surface of the target material have a ballistic impact and return to the substrate, causing Re-sputtering. The average number of atoms ejected from the surface of the target material by the collision of each ion is called the Sputter Yield.
The sputter yield depends on many factors, such as:
- The angle at which the ions strike the surface of the target material
- The amount of ion energy during the collision
- The weight of the ions
- The weight of the atoms of the target material
- The binding energy between the atoms of the target material
- Magnetic field strength and design factors (in magnetron cathodes)
- Plasma gas pressure
A table of sputtering yields of several material is displayed in Table 1. The numbers vary under different deposition conditions as mentioned earlier, but are useful for comparison purposes.
If the structure of the target material is crystalline, the orientation of the crystal axis relative to the surface is also an important factor in the sputtering yield.
Deposition
One of the applications of sputtering phenomenon is Deposition. Sputtering deposition is a method of creating thin films of a few nanometers to a few micrometers on the desired substrate. In this process, the atoms separated from the surface of the target material are gaseous. These thermodynamically unstable atoms tend to be on a surface in a vacuum chamber. The atoms on the substrate which form a layer with a few nanometers to a few micrometers thick, is called a Thin Film.
Physical Vacuum Deposition Method
This type of deposition is a physical vacuum deposition method (Physical Vapor Deposition). PVD is a set of deposition methods in which the material enters the vapor phase from the dense state and returns to the dense phase as a thin film.
These vacuum deposition methods include three stages:
- Evaporation of the target material
- Transfer of vapor from the target material to the substrate
- Formation of a thin film on the substrate with accumulation of vapor of the target material
Sputtering Process
In order to vacuum coating by sputtering technology, ions need to be fired at the target material in the plasma medium. The gas to be used in the sputtering process must have two properties: first, that its atomic weight must be such that it can affect the atom of the target material, and second, it must not chemically react with the target material. According to the mentioned cases, the gases used in the Sputtering Process are from the group of noble gases in the last column of the periodic table (Argon, Xenon, etc.). Argon gas is the most common gas used in this process.
Gaseous plasma is a dynamic environment in which neutral gas atoms, ions, electrons, and photons are in near equilibrium. Since the plasma energy is transferred to the surrounding area, a DC or RF power source should be used to form a sustainable plasma. Plasma is formed by injecting a noble gas (usually Argon) into a vacuumed chamber until it reaches a certain pressure (maximum 0.1 Torr) and applying DC or RF voltage.
Sputtering Rate
Sputtering rate is the number of monolayers per second sputtered from the surface of a target. It depends on the sputter yield (S), Molar weight of the target (M), material density (p), and ion current density (j), as represented in Equation (1):
Sputtering rate = (MSj)/(pNAe) Equation (1)
Where NA is the Avogadro number and e is the electron charge.
GLAD Sputtering
GLAD (Glancing Angle Deposition) sputtering is used in the deposition of microstructures mainly designed for optical devices. In this method various columnar or spiral nano/micro structures can be created by means of setting different substrate tilt angles and rotation speeds against the target.
Ion Beam Sputtering (IBS)
In this method the target atoms are sputtered by a focused high energy ion beam. The Argon ions are generated and accelerated inside a low vacuum ion source and leave it toward the target in a high vacuum environment (about 10-4 Torr), with a pressure lower than what is required in a typical sputtering process chamber. This method allows sputtering deposition under lower impurity condition.
Ion Assisted Sputtering (IAD)
This method, which is an upgraded IBS method, makes the reactive sputtering possible by applying a secondary ion source directed onto the substrate. With introduction of non-inert gases like O2 and N2 and a second plasma formation, the sputtered target atoms react with the plasma and layers of metal oxide/nitride are deposited on the substrate.
Diode Sputtering
In diode sputtering, an electric potential difference is applied between the target and the substrate to form a plasma discharge inside a low vacuum chamber. The free electrons in the plasma are immediately removed from the negative potential electrode (cathode). These accelerating electrons collide with neutral gas atoms (Argon) in their path, causing the electrons in the shell of these atoms to separate. As a result, the gas atoms become positive ions and accelerate towards the cathode, causing the sputtering phenomenon. Glow discharge occurs when some of the positive ions return to their ground state by adsorbing free electrons and releasing photons.
This mechanism is called Diode Sputtering and the applied voltage can be DC (with constant poles) or RF (with alternating poles), depending on the target material. One of the problems with this method is that its coating rate is low and it takes longer to do the coating, which causes the target to heat up and damage its atomic structure, which is improved utilizing Magnetron Cathodes.
Magnetron Sputtering
With the advent of magnetron sputtering method, the problems for diode sputtering were solved. By placing a number of magnets behind the cathode, the free electrons are trapped in the generated magnetic field just near the target surface. These electrons do not reach the substrate like the diode sputtering method and do not bombard the substrate surface.
The movement of these electrons in the path of the curve led by the magnetic field increases the probability of ionization of the neutral gas atoms many times over. Increasing the ions that hit the surface of the target intensifies the rate of deposition.
Vac Coat is a designer and manufacturer of PVD systems that most products use magnetron sputtering methods, such as Desk Sputter Coater (DSR1), and Magnetron Sputter Coater (DST1-170 and DST1-300).
In addition, Vac Coat produces hybrid systems like Sputter Coater and Thermal Evaporator (DST3-T and DST3), Sputter and Carbon Coater (DSCR, DSCT, DSCR-300, and DSCT-T), which are equipped with magnets behind the cathode and perform magnetron sputtering.
Both Diode and Magnetron sputtering methods can be performed with DC or AC (radio frequency, RF) voltages, depending on the target material.
DC Sputtering
DC Sputtering is suitable for metals and materials that are electrically conductive. The DC power supply used in this method is less complex and more controllable than other power supplies, and has a lower manufacturing cost.
This is why DC sputtering is the most popular sputtering method in terms of power supply. The Desk Sputter Coater (DSR1) made by Vac Coat Ltd. is a simple system that has a lower price than other models. This device is only capable of DC sputtering.
RF Sputtering
In RF Sputtering an alternative voltage, with a frequency in the range of radio waves, is applied to the cathode instead of the DC voltage used in a typical DC sputtering. This results in continuous changing of negative/positive pole that prevents charge accumulation on the surface of insulating targets. With this technique, magnetron sputtering of non-conducting is made possible, and arcing plasma during deposition is avoided.
Vac Coat sputtering systems like high-vacuum single-target sputter coater (DST1-300) and triple-target sputter coater (DST3) with thermal evaporator (DST3-T) are equipped with 600W DC power supply, 300 W RF power supply (optional) with auto matching box. Also, these models are supplied with a plasma cleaning option to clean substrate surfaces through plasma treatment.
The DST3-T, Triple Target Turbo Pumped Sputter Coater, is a multi-vacuum coater system that combines thermal evaporator and sputter coater in one single compact desktop system. The high vacuum system is suitable for deposition of a wide range of materials.
These high vacuum sputtering systems can deposit a wide range of target materials, including metals, metal-oxides, semiconductors, and ceramics on different surfaces for various thin film applications and FESEM sample preparation. For more information, you can see RF Sputtering post and if you are interested in types of electron microscopes like SEM, TEM, follow the links below.
Confocal Sputtering
If the deposition process is performed from several cathodes, the Confocal Sputtering Technique can be used. In this technique, the cathodes are arranged in a circular pattern with a focal point. By placing the substrate that rotates around its axis at or around the cathodes focal point, a layer is deposited that has a much better uniformity than the layer deposited using a cathode. Also, this technique is effective to perform the deposition of several different materials simultaneously for alloying (Co-Sputtering) or asynchronous to create multi-layers.
Using this technique, a uniform layer can be obtained on a substrate with a diameter twice the diameter of the target. Also, for materials that have low sputtering yield, the deposition can be applied using several cathodes simultaneously at a higher speed. The Triple Target Sputter Coater manufactured by Vac Coat Ltd. models DST3-A and DST3-TA equipped with three angled and focal cathodes, are able to perform Confocal Sputtering.
Reactive Sputtering
In this type of sputtering, the atoms separated from the target undergo a chemical reaction before being deposited on the substrate. The resulting deposited thin film will have a different composition than the target material composition. Chemical reaction occurs between the atoms separated from the target and reactive gases (such as Oxygen or Nitrogen) that enter the vacuum chamber during the deposition process.
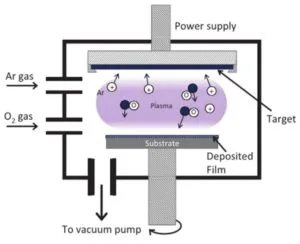
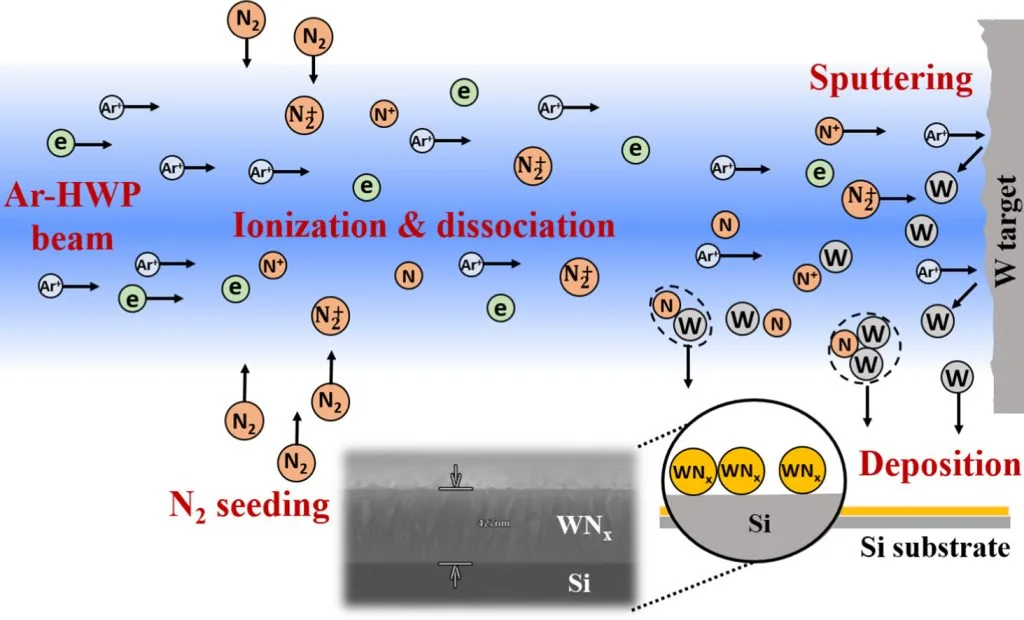
By adjusting the amount of inlet gases and noble gas (Argon) used in this process, a thin film with the desired composition and stoichiometry can be deposited. The Vac Coat company has various models of Vacuum Coating Systems, such as DST1-300 and DST3, with one or more inlets installed for reactive gas flow into the vacuum chamber during the deposition process.
High Power Impulse Magnetron Sputtering (HIPIMS)
HIPIMS is a new Magnetron Sputtering Method that uses high power pulses to increase target ionization. Compared to conventional magnetron sputtering, this method ionized atoms reach the substrate with more energy, which increases the density and quality of the deposited thin film.
High-Target-Utilization Sputtering (HiTUS)
The gaseous plasma can be generated in a chamber other than the main one and then introduced and guided to the target in the deposition chamber by DC electromagnets. This method has the advantage of uniform corrosion of the target during sputtering process, which results in higher target utilization of near 95% compared to a typical DC/RF sputtering.
VacCoat Ltd. is the manufacturer of a wide range of PVD systems, employing sputter coating technology to achieve nanometer thin films for a variety of applications.
Vac Coat Sputter Coaters
Vac Coat Ltd. produces various models of Vacuum Coating Systems to perform Sputtering Deposition Process. These systems are classified into different models depending on the ultimate pressure they can reach, the power supply used in them for the sputtering process, the number of cathodes, the dimensions of the vacuum chamber, etc. For more information about the Vac Coat Ltd. products, please visit Vac Coat (You can read more about our sputter coaters here).
Reference
- http://www.ajaint.com/what-is-sputtering.html
- http://www.semicore.com/what-is-sputtering
- https://en.wikipedia.org/wiki/Sputter_deposition
- https://www.angstromsciences.com/sputtering-yields
- Bundesmann, Carsten, and Horst Neumann. “Tutorial: The systematics of ion beam sputtering for deposition of thin films with tailored properties.” Journal of Applied Physics 124.23 (2018): 231102.
- https://polygonphysics.com/applications/ion-beam-sputter-deposition/
- Bairagi, Samiran, et al. “Glancing angle deposition and growth mechanism of inclined AlN nanostructures using reactive magnetron sputtering.” Coatings 10.8 (2020): 768.
- https://www.specs-group.com/fileadmin/user_upload/products/technical-note/sputter-info.pdf
- https://www.horiba.com/int/scientific/applications/material-sciences/pages/gdoes-the-analytical-companion-tool-for-magnetron-sputtering-deposition/
- https://ebrary.net/191961/engineering/reactive_sputtering
- Tiwari, Atul. Handbook of antimicrobial coatings. Elsevier, 2017.
- Doghmane, N. E. A., et al. “Confocal magnetron sputtering deposition of Cu/AZO bilayer structures: effect of Cu thickness on microstructural and optoelectronic properties.” Journal of Materials Science: Materials in Electronics (2022): 1-11.
- Ghazal, H., & Sohail, N. (2022). Sputtering Deposition. Thin Film Deposition – Fundamentals, Processes, and Applications [Working Title]. doi: 10.5772/intechopen.107353
- WNx thin film-Huang, Tianyuan, et al. Sputter deposition of WNx thin films by helicon-wave-excited argon plasma with N2 seeding. Surface and Coatings Technology 410 (2021) 126941.
Hi Vaccoat
What factors affect sputtering rates for coating with different targets?
Sputtering deposition rate is related to many factors like process pressure, exposed power to the target and sputtering yield of the target. For example, the sputtering rate for Cr could be 10nm/min and for the gold 40nm/min.
Good evening
I did not get very well. What is the effect of target thickness on the magnetron sputtering process?
Dear Marcus, the magnetron sputtering deposition depends on the strength of the magnetic field. This magnetic field is nonhomogeneous and is changing with the target thickness. The thicker the sputtering target, the lower the magnetic field at the target surface, which reduces the concentration of charged particles in the plasma and results in a lower deposition rate.
Could you explain it in detail “What is pre-sputtering?”, please?
Hi dear Ana.Sure, in case of using oxidizing targets, or if the target surface is slightly contaminated, usually a pre-sputtering process is performed. During pre-sputtering, the target is bombarded with heavy Argon ions to remove oxygen and contaminations from the target surface for a limited time (about 2 minutes) while the shutter is closed to protect the substrate from unwanted coating.
Hello Vaccoat
What is noble metal target surfaces reactivity with the working gas in the chamber during sputtering process?
Noble metal targets like gold, platinum, and the other platinum group metals (ruthenium, rhodium, palladium, osmium, and iridium) are mostly regarded as metallic chemical elements that are resistant to corrosion and are usually found in nature in their raw form. For metals like copper, silver, and gold, their full d-subshells contribute to what noble character they have. In contrast, the other noble metals, especially the platinum group metals, have distinguished catalytic applications, resulting from their partially filled d-subshells. This causes difference in reactivity on noble metals, which can be seen during the preparation of clean metal surfaces in an ultra-high vacuum: surfaces of noble metals like gold are easy to clean and keep clean for a long time, while those of platinum or palladium, for example, are covered by carbon monoxide very quickly.
What is cold sputtering?
The sputtering deposition of thin films without active substrate heating and with reduced passive heating by cathode is called cold sputtering. However, it should be noticed that temperature rise depends on several other factors, e.g. incident power density, sputtering current, deposition time, distance between source and substrate, efficiency of cooling system.
Why Argon is mainly used as the process gas in the sputtering process?
“Argon gas is favorable in the sputtering process due to several reasons:
Large atomic mass of Ar atoms results in more efficient sputtering of target material.
Low chemical reactivity of Ar atoms with target material leads to higher purity of the resulting layer.
Argon gas is relatively low cost in contrast to other inert gases.”
¿qué fenómenos físicos ocurren al incidir las partículas energéticas sobre un sustrato sólido para formar las películas delgadas?
This thin film deposition technique is called Ion Beam Assisted Deposition (IBAD) and is discussed on our blog page https://vaccoat.com/blog/ion-beam-sputtering-ibsd/.
What is the hardness of the coated Pt or Au on a aluminum part? Just want to know if this can be scratch free with electrode contact.
The coating hardness strongly depends on the chosen deposition method and parameters, such as pressure, layer thickness, substrate heating or applying bias voltage during thin film deposition. You can refer to the scientific literature for more detailed discussions on this issue.