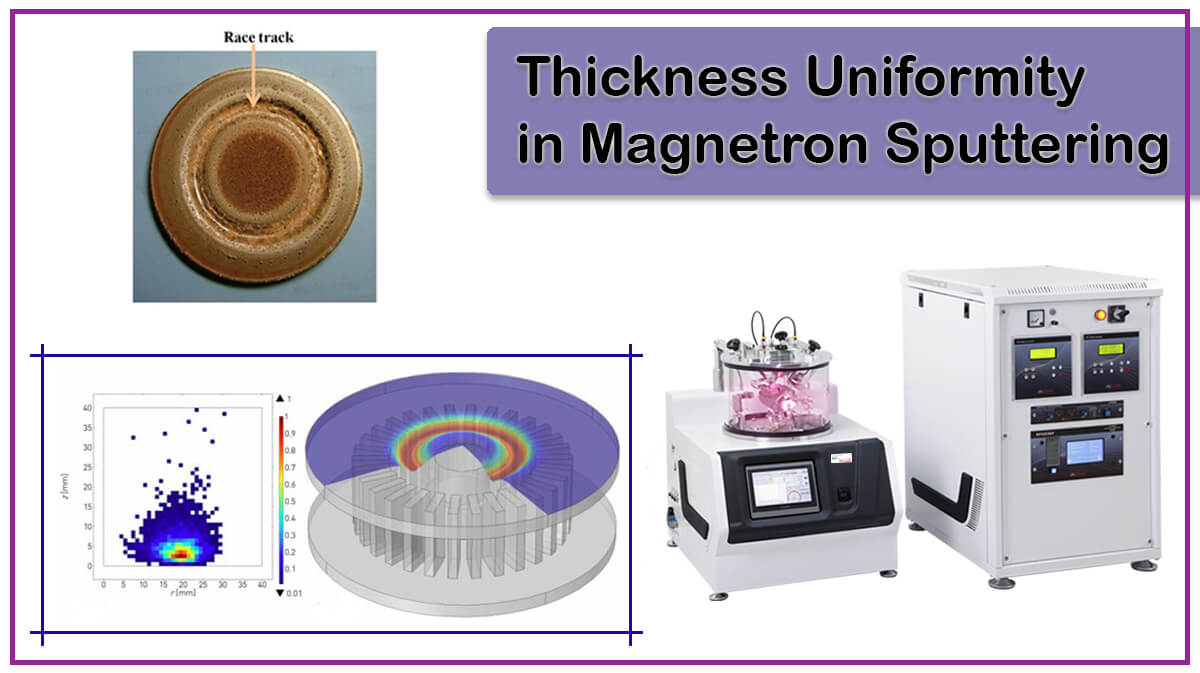
Thickness Uniformity of Thin Films by Magnetron Sputtering
Magnetron Sputtering is a highly advantageous method for depositing thin films of materials on a substrate for research and industrial purposes. Thickness Uniformity of thin film distribution is an important parameter in science and industry, which can be obtained by magnetron sputtering to a high degree of precision (<2% of thickness variation over the substrate) [1]. In addition, Vac Coat Sputter Coaters can sputter materials by Magnetron Sputtering Method.
However, some processes during deposition affect thickness uniformity of the resulting layer in magnetron sputtering. Based on theory, the uniformity of thin-film thickness deposited by magnetron sputtering can be investigated by considering the effect of geometric parameters such as target-substrate distance, ion energy, target erosion area, temperature, and gas pressure.
Target surface homogeneity influences uniformity of deposited layer as investigated by several research groups. Charged particles created as a consequence of ion bombardment of target, tend to swirl above the target in the presence of magnetic field, undergo collisions with argon atoms and produce more free electrons and Ar+ ions (Figure 1. Left). Charged particles confined to the target surface by the magnetic field collide with target, where erosion occurs (Figure 1. Center and Right).
Magnetic confinement of energetic electrons in magnetron sputtering increases ionization and sputtering rate at lower operating pressure and higher deposition quality, while suffers from drawbacks such as non-uniform ion flux onto target, non-uniform target erosion and reduced target utilization (typically 20-40%).
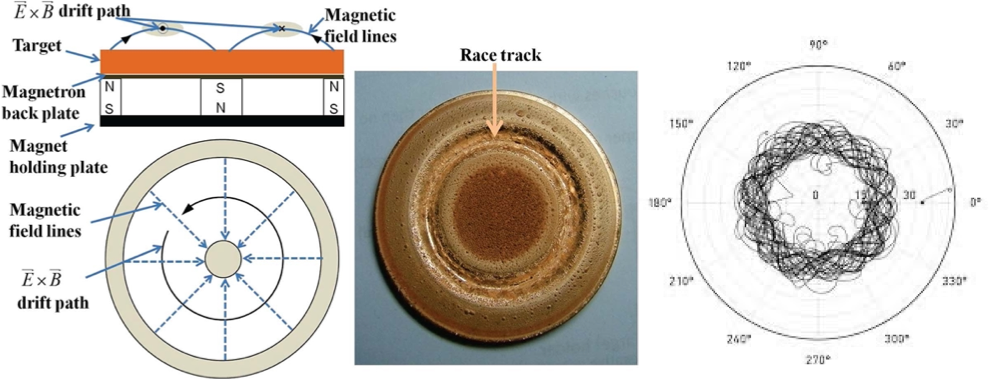
Collisions occur randomly when scattered particles move from the target to the substrate. The probability of this scattering is given by Equation (1):
(1) K= e^((-d)/λ)
Here d is the distance, λ is the mean free path of a particle, and K is the probability of particle scattering. As shown in Figure 2, applying an electromagnetic field changes the distribution of the electrons and a saddle-etched profile appears on the target surface, confirming that the sputtering rate is not constant at the target surface.
In general, finite element based on magnetic field distributions are used to obtain the etching rate distribution of the etch ring. The Gaussian distribution of Equation (2) is used to simulate the depth of the etching ring.

(2) Y=A e^(〖-x〗^2/2(c^2))
Where A is the etching depth, c is the etching width coefficient, Y is the etching depth distribution, and x is the coordinate of each point in the horizontal direction of the etching ring.
Angular Distribution of Target Particle Sputtering
At present, a cascade collision model based on momentum transfer theory can better explain the phenomenon of high-velocity particle bombardment that causes target particles to be sprayed. When the energy of radiative particles is high, almost all emissions are normal at the target level and virtually none are lateral. In contrast, the number of particles scattered near the target surface increases when the energy of the particles is low. As shown in Figure 3, the angular distribution curve is assumed to be an elliptical distribution.
Based on Equation (3), the angular distribution of sputtering is investigated:
(3) S(θ)=(2m cos 〖(θ)〗)/(α^2+(1-α^2)cos ^2〖(θ)〗)
Where θ is the angle between the particle sputtering direction and the normal direction (Z direction) of the target surface, α = m / n ellipse coefficient, m ellipse length in the normal direction (Z direction) of the target surface, and n small axis of the ellipse in the tangential direction (X Direction).

Thickness Distribution with Fast and Slow Particles
In magnetron sputtering, due to the effect of gas pressure, the deposited particles can be roughly divided into fast particles (which do not collide) and slow particles (which collide). Rapid particles represent particles that reach the substrate surface directly without any impact after sputtering, and slow particles represent particles that reach the substrate surface by diffusion with impact scattering. Equations 4 and 5 (Figure 3) below show the number of fast particles and the number of slow particles deposited per unit area on the substrate.

Target Shape
Here we investigate effect of target shape on the uniformity of deposited layer thickness distribution:
Round Target
In general, film thickness distribution T in magnetron sputtering systems is proportional to the growth rate at each point of the substrate, formulated in the Equation 6:
(6)
Where c2=a2+b2, b2=R2+r2-2Rrcosφ. Geometrical parameters are shown in Figure 4, cos^n(θ) characterizes spatial distribution of the flow of sputtered atoms and Ψ(R) describes cathode erosion rate. [4]
Where Yt is the number of particles scattered per unit area of the target, (xt, yt) the coordinates of a point on the target, and κ is the diffusion coefficient (m^2/s).
In the total thickness, we must consider both fast and slow particles. From Equations (4) and (5), it can be seen that the uniform distribution of layer thickness is affected by geometric parameters: target-substrate distance, temperature, gas pressure, the electromagnetic force, and other factors. For the target, it is important to define the geometric parameters of the erosion area, as they directly determine the overall thin film deposition process. To simplify the model, the following hypotheses are necessary:
- Erosion zone features
- Dynamic properties of particles that are constant in the coating process, ie. sputtering conditions, current density, diffusion and transport of dispersed particles are constant. In general, the shape of the erosion zone is a function of time. When the target material is eroded, it shows a complex three-dimensional surface in macroscopic terms

Here we have brought the data on calculated thickness uniformity due to different target-substrate distance in Figure 5, which presents that with increasing target-substrate distance, more uniform deposition can be obtained. As shown in Figure 5, sputtering power and working pressure have inessential influence on the deposited film thickness distribution.

Rectangular Target
For rectangular target we will have the following assumptions to investigate the relation between thickness uniformity and target erosion area:
Here We consider copper as the target material and argon as the sputter gas. The energy of dispersed copper atoms is usually reported to be less than 10 eV. Therefore, the free mean length for copper atoms is equal to:
λcu=3.45×10^(-4)×(T/P)
For a temperature of 300 K and a pressure of 1 to 5 Pascals, the free mean path of copper atoms is 21 to 138 mm.
Considering the percentage length as the ratio between the length of uniform area on the substrate and the substrate length to judge the thin film thickness uniformity under different target conditions. The uniform area is an area where the thin film thickness has less than 5% non-uniformity.
Length percent=(The length of uniform deposition zone on the substrate/The substrate length)
In the following, we will examine the change of the target-substrate distance from 30 mm to 80 mm. Considering the sputtering yield (Y) as 1.5 atoms per ion, the current density of 2 mA/cm2 and the free mean path of the copper atom of 40 mm, from Figure 6, it is easy to see that when the substrate relatively moves towards the target and the distance changes from 30 mm to 80 mm, the percentage of uniform length decreases accordingly. As a result, the thickness of the thin film increases with decreasing target-substrate distance. The beta factor in this chart is the fitting factor.


Similarly, as Figure 8 shows, when the free mean path has different values, the functional relationship between the target-substrate distance and the length percentage varies. The general trend presented in Figure 8 is similar to Figure 6, ie as the target-substrate distance increases, the percentage of uniform length decreases. When the free mean path changes from 80 mm to 40 mm, the pressure increases or the temperature decreases accordingly, which corresponds to the result that the deposition rate decreases with increasing pressure.
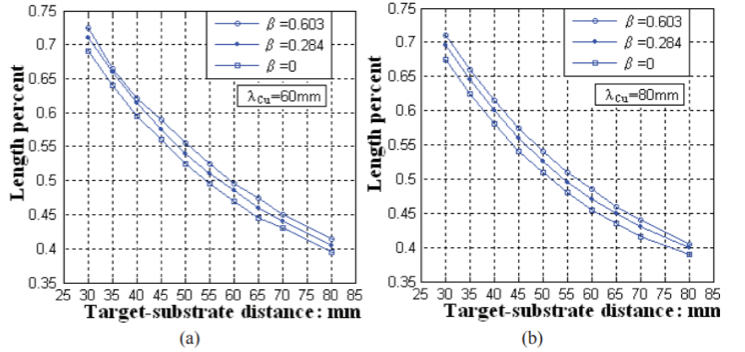
The calculation shows that a proper reduction of the end-erosion zone (Δ) for a rectangular target also reduces the thickness uniformity. Conversely, a proper increase in the end-erosion area increases uniformity. Meanwhile, when Δ reaches a certain value, as shown in Figure 9 (b), the uniformity first increases and then decreases with increasing target-substrate distance.

It can be concluded that the deposition rate is largely influenced by the size of the erosion zone, while the magnetron power, the target material and the pressure do not affect the distribution process. Thickness uniformity decreases with increasing distance of the target substrate and decreasing the erosion zone of the end of the target.
As the erosion zone of the end of the target increases somewhat, the uniformity increases and then decreases as the target-substrate distance increases. There are two tendencies for thin film thickness uniformity with increasing length to width ratio of the target erosion area, ie it decreases slightly when the length is constant or increases when the width is constant. And the thickness of the thin layer decreases with decreasing power and increasing gas temperature. The deposition rate increases with decreasing target-substrate distance or increasing power and temperature.
Vac Coat Sputter Coaters
Vac Coat Ltd. is known for designing and manufacturing high-quality and reliable Physical Vapor Deposition and vacuum coating systems. Its products include sputtering systems, carbon coating systems, thermal evaporation systems, and pulsed laser deposition system. All Vac Coat Sputter Coaters are able to deposition by magnetron sputtering method and some of them can create Cu thin films by DC Magnetron Sputtering.
The Sputter Coaters include sputter coater with a thermal evaporator (DST3 & DST3-T), magnetron desk sputter coater (DST1-300 & DST1-170), and turbo pumped desk sputter and carbon coater (DSCT & DSCT-T), that equipped by Turbomolecular Pump. For more information, visit the website please.
Related Posts
References
- M. Geisler, Ch. Braatz, J. Bruch, A. Kastner, M. Kress, M. Ruske, T. Willms, A. Zmelty, Meeting the demands of modern large area glass coating: latest developments of horizontal and vertical coaters and applications, Thin Solid Films, Volume 442, Issues 1–2, 2003, Pages 15-20, https://doi.org/10.1016/S0040-6090(03)00931-3
- Performance of a size-selected nanocluster deposition facility and in situ characterization of grown films by x-ray photoelectron spectroscopy,Review of Scientific Instruments 85, 065109 (2014) http://dx.doi.org/10.1063/1.4882315
- Feist, Christian, A. F. Plankensteiner and Jörg Winkler. “Studying Target Erosion in Planar Sputtering Magnetrons Using a Discrete Model for Energetic Electrons.” (2013).Proceedings of the 2013 COMSOL Conference in Rotterdam
- Soloviev, A. A., N. S. Sochugov, K. V. Oskomov, and N. F. Kovsharov. “Film thickness distribution in magnetron sputtering system with the round cathode.” Изв. вузов. Физика 8 (2006): 491-493.
- Coatings 2021, 11, 599. https://doi.org/10.3390/coatings11050599
- ZHANG Yichen et al. / Physics Procedia 32 ( 2012 ) 903 – 913