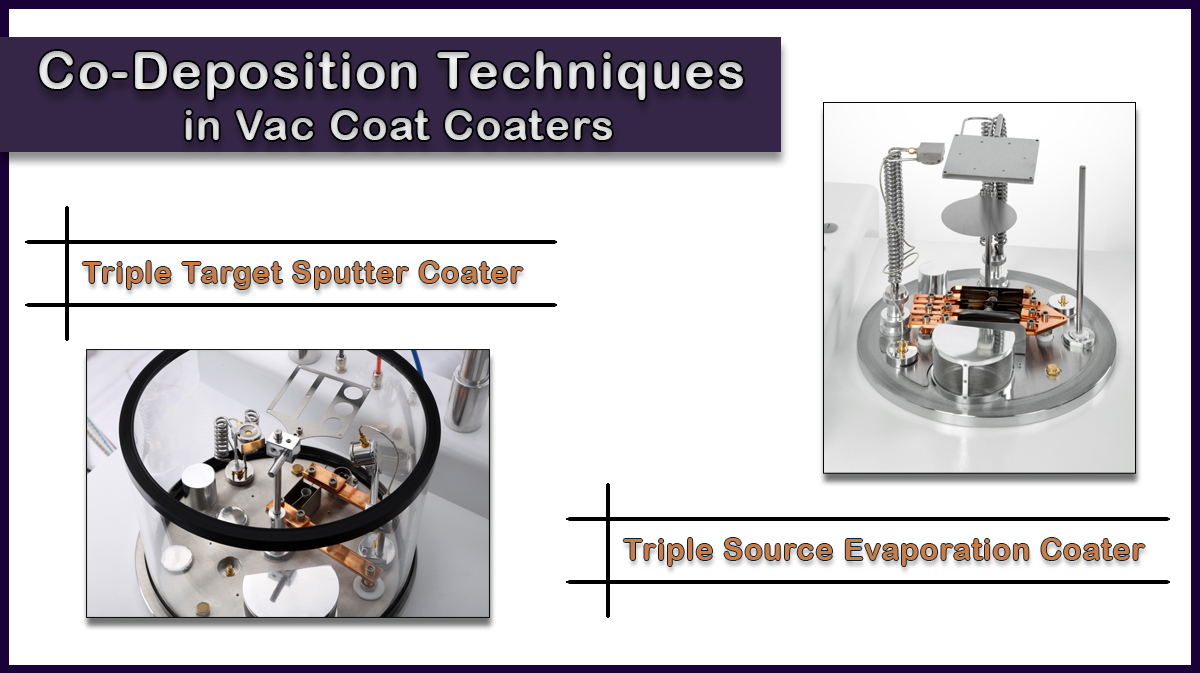
Co-Deposition Techniques in Vac Coat Coaters
After the scientific revolution driven by nanotechnology, nanocomposites, and hybrid materials with many applications play a vital role in modern science and technology research. These kinds of materials offer electrical and mechanical properties, optical interaction, and thermal conductivity with very high efficiency. The vital part of nanocomposites research is choosing the best way to prepare these complex materials. Co-Deposition Techniques indicates a procedure with two, three, or more deposition sources. Thus, these different or same sources react together and coat on the desired samples to provide alloys and hybrids with excellent characteristics.
Co-Deposition Types
The bellow co deposition techniques are used for manufacturing fantastic composites:
- Electrolytic co-deposition
- Co-sputtering
- Co-evaporation
- Spray co-deposition
In the following, we want to devote our attention to co-sputtering and co-evaporation because they will produce large-scale production to achieve real require applications. These most popular Physical Vapor Deposition processes are run in a vacuum chamber and offer various applications in biological sensors, optical instruments, nanomedicine, electronics, and nanoengineering.
Co-Sputtering
Co-sputtering is a coating from multiple sputtering targets (or sources). The constructions and alloys produced with co-sputtering cannot be coated in a single source. Co-Sputtering that can occur sequentially or simultaneously in the vacuum chamber from multiple targets is used for depositing compositions for various applications. In this method, the formation of a multi-layer or composites are achieved through some steps; sputter the first target separately and then sputter another one to deposits respectively, or sputter all of them along with each other simultaneously.
Remarkably, by multi-source sputtering deposition, you could change materials and targets during a deposition to prepare structures for desired research aims without opening the chamber or breaking the vacuum.
Co-Sputtering Applications
The applications of multiple-target co-sputtering are developing. The primary usage of these systems is preparing compounds, alloys, or composites in practical film formation for solar panels and displays and a wide range of sensors. In co-sputtering, the stoichiometry is controlled by optimizing the power and place of each target separately. If you sputter alternately, you finish with a multilayer with periodic structures that depends on your sputtering time.
Vaccoat Ltd. is a worldwide supplier of sputtering equipment and offers the Co-Sputtering Coater named is DST3. This triple target sputter coater provides RF and DC power supplies to sputter a wide range of metals, semiconductors, and dielectrics with a large vacuum chamber and water-cooled cathodes. the DST3 uses three cathodes in the vacuum chamber, and each cathode could be controlled by a different power supply separately.
DST3 Coater can use three cathodes with the same target material to increase deposition yield, also can mix different types of targets in one process to create individual compositions with specific properties. The technical architecture of co-sputtering coaters strongly depends on the desired application.
- Sputter Coater model DST3-A deposit materials with the use of three confocal angled cathodes to produce the desired composite very easily, control compound coatings, and decrease target consumption.
- Sputter Coater model DST3-S using 3 straight cathodes. So in this device, you could achieve a very uniform deposited layer.
- Sputter Coater model DST3-T offers the 3-cathodes sputter coater with the thermal evaporation head to save laboratory space and money.
- Vac Coat suppliers designed the DST2-A model with only two angle cathodes to customize co-sputtering systems at a lower price.
Moreover, all Vac Coat Coaters are equipped with motorized rotating sample holders to increase uniformity and smoothie of the deposited layer.
Co-Evaporation
Comparing to Sputtering, Thermal evaporation has reasons to support and oppose:
In the Co-Evaporation process, each source of materials (boat or basket) is heated separately in a high vacuum environment to melt and then evaporate; after that, the vapor phase of materials reacts to each other to deposit on the substrate. The sample could be heated or being rotated in thermal evaporation for increasing uniformity during the vacuum deposition.
Co-Evaporation Applications
The applications of Co-Evaporation thin films are in the preparation of a multilayer on metals, glass, plastics, and any other substrates. These layers could offer reflectivity and opacity for solar cells, telescope technology, etc. Perovskite solar panels that are produced by Co-Evaporation techniques show an efficiency of more than 20%.
One approach to perovskite layers preparation is thermal co-evaporation with three evaporation sources. Vac Coat provides a multi-source thermal evaporation coater with the name of DTT to offer co-evaporating. This coater is equipped with a motorized standard rotation sample holder.
Co-Sputtering VS. Co-Evaporation
- Co-Sputtering performs high-speed charged atoms to bombard the target. So, this process needs high voltage and expensive power supplies. On the other hand, thermal evaporation needs high current power supplies.
- Co-Sputtering may damage substrate with high-speed charged particles that generate in a plasma environment. However, the high-energy atoms in thermal evaporation are lower than sputtering because these atoms in thermal evaporation use energy to evaporating instead of accelerating. As a result, substrate-damaging decreases in co-evaporation.
- Eventually, co-sputtering shows better adhesion compare to co-evaporation.
Hi
How to deposit LLZO (Lithium garnet) thin films by sputtering and maintain desired stoichiometry?
Normally, heating is needed to obtain LLZO with desired structure, while the the heating process results in lithium defeciency. With confocal sputtering of LLZO (Lithium garnet) and LiO2 (Lithium oxide) targets the sputtering rates are optimized to tune the over lithiation of the thin film before heating, which compensates for the lithium loss during heating, thus achieving required stoichiometry. Vac Coat DST3-A sputter coater with RF power source is able to do confocal sputtering of non-conductive targets like LLZO and LiO2 with Cu backplates.