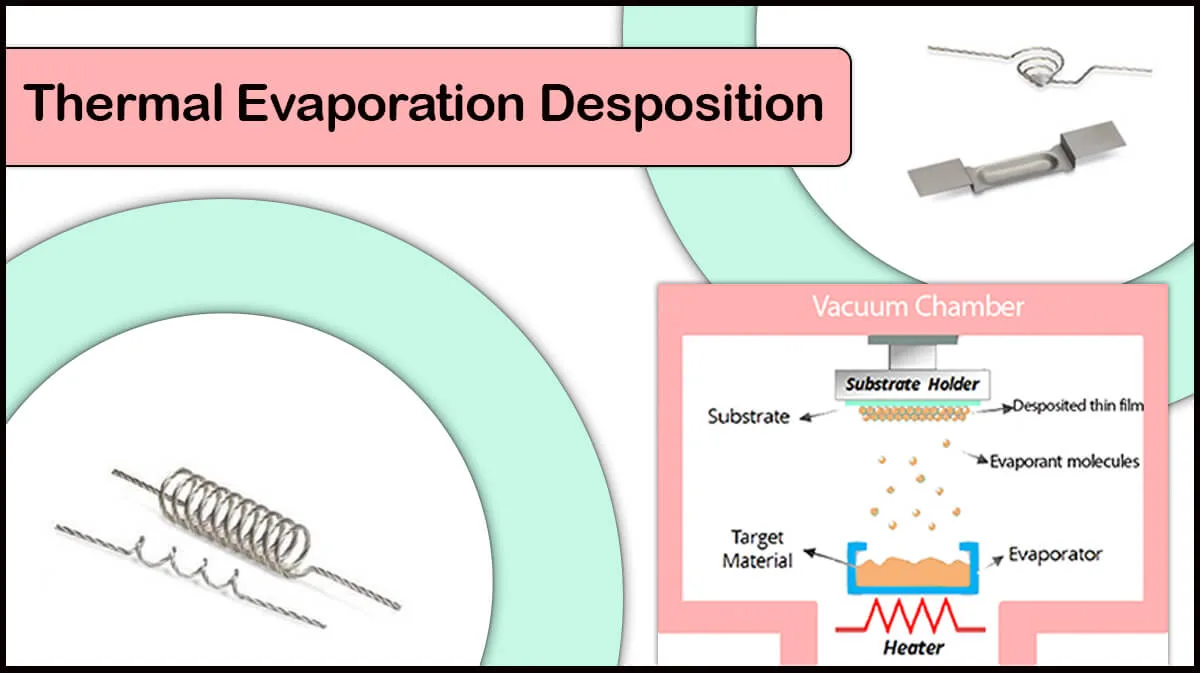
What is Thermal Evaporation?
Thermal evaporation is one of the most popular vacuum deposition method due to its notable merits like simple operation process and proper speed. The thermal evaporation process is one of the physical vapor deposition (PVD) methods in which a thin film of a heated source material is deposited onto the substrate. Different vacuum evaporation methods are named after the various thermal evaporation techniques, such as resistive thermal heating, electron beam evaporation, laser beam evaporation (As pulsed laser deposition method), molecular beam epitaxy (MBE), arc evaporation, and ion plating evaporation.
Thermal Evaporation Mechanism
In the process of thermal evaporation method of thin film deposition, the target material is located inside an evaporation source (Boat, coil, and basket) which is heated by the passage of an electric current. The target material inside the evaporation source is heated to the evaporation point. Because heat generation is due to the electrical resistance of the evaporation source, this method is also called resistive evaporation.
After evaporation, the molecules of the target material move to the substrate and form a thin film on the surface of the substrate. Many materials can be deposited using this method, including Aluminum, Silver, Nickel, Chromium, and Magnesium, as well as amorphous chalcogenide films such as CdSSe, MnS, Ge-Te-Ga, and so on, appropriate for memory-switching applications, phase-change materials, and solar cell fabrication.
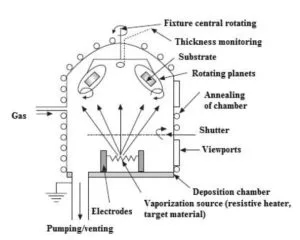
High-Vacuum Deposition
One of the important features of vacuum evaporation systems is their ultimate pressure. In the process of evaporation for thin film deposition, if the evaporated molecules of the target material in their path to the substrate collide with the molecules of gases in the chamber, they will undergo undesired changes in their path and this will negatively affect the quality of the sample coverage. To prevent this, the thermal evaporation deposition process must be performed in a high-vacuum environment.
At a pressure of 10-5 Torr, the mean free path length of the molecules, the average distance traveled by the molecules in the vacuum chamber before colliding with another molecule, is around 1 meter. As a result, it can be said that the molecules of the vaporized material can reach the substrate in a straight line without colliding with other molecules.
On the other hand, the presence of background gases in the deposition chamber may contaminate the deposited thin film. For example, the presence of a small amount of oxygen or moisture during thermal evaporation in the process of Organic Light-Emitting Diode (OLED) and organic photovoltaic device fabrication, makes the active functional parts of these devices inefficient. By reducing the pressure of the deposition chamber to 10-6 Torr, the purity of the deposited thin film and the performance of the devices will increase significantly.
Applications of Thermal Evaporation Deposition
Thermal evaporation deposition has a variety of uses, including the following:
- Creating metal bonding layers in devices such as OLEDs, solar cells, and thin film transistors
- Create a thin film of Indium on the back of the ceramic sputtering targets to connect the metal backing plate
- Deposition of metal thin film (Often aluminum) on polymers for use in food packaging, as well as heat and sound insulation purposes
Polymer films coated with a thin layer of metal such as aluminum using the thermal evaporation deposition method, namely metalized polymer films, have aluminum foil characteristics as being shiny but are lighter and cheaper in contrast, utilized for decorating purposes, packaging food products, heat reflection (As in NASA spacesuits and firefighter uniforms).
What Are the Thermal Evaporation Advantages?
- No substrate heating is required
- High-rate film deposition (Around 500 nm per minute)
- Little surface damage as a result of low energy atoms (0.1 eV)
- Low impurity incorporation due to a high-vacuum environment
What Are the Thermal Evaporation Drawbacks?
There are several shortcomings that thin Film deposition by thermal evaporation suffers, like:
- The process is limited to the low melting point metals and compounds
- Small filament size limit the deposition thickness
- Due to weak adhesion between the substrate and gold atoms, Cr coated substrate is required for gold thin film deposition
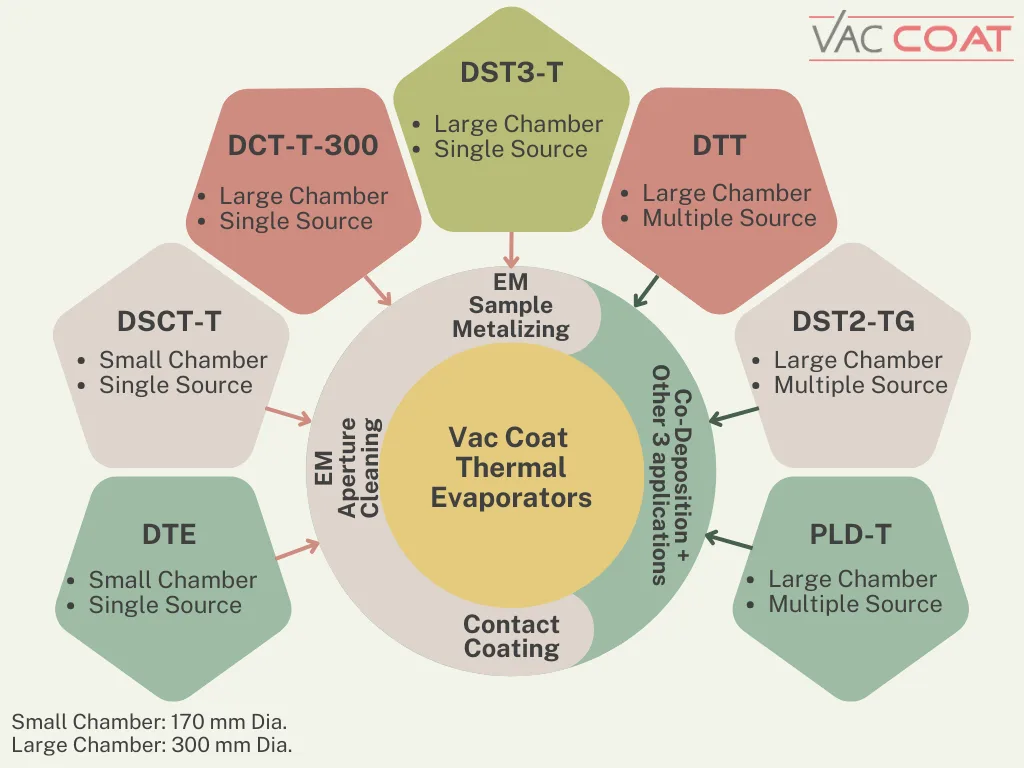
Thermal Evaporation Deposition Systems
Thermal evaporation deposition devices contain several parts, including:
Vacuum System:
The evaporation deposition systems require a high-vacuum chamber for an efficient thin film deposition. Turbo Molecular and diffusion pumps are commonly used to establish a high-vacuum chamber. The turbo molecular pump (TMP) used in the Vac Coat high-vacuum coating systems is supplied by Leybold, a German company. TMPs are much smaller and reduce the required time to reach the desired pressure in a thermal evaporation process, while not needing cooling water and oil, eliminating possible returning of the oil to the vacuum chamber, with the same efficiency compared to the diffusion pumps.
Evaporant Sources:
The metal and compound materials in the form of wire, pellets, etc are loaded onto heating elements referred to as evaporation sources like boats, baskets, or coils due to their shape. When a large current passes through the resistive filament containing the material to be deposited, it is melted and evaporates into a cloud above the source.
The evaporation sources can be made from tungsten wires in the form of filaments, baskets, heaters, or coils. Boat-type evaporation sources are usually made from high-temperature melting materials such as tungsten, tantalum, molybdenum, etc.
Vac Coat Desk Thermal Evaporators: DTE and DTT
Desktop turbo pumped thermal evaporation deposition systems, DTE and DTT, are vacuum deposition systems suitable for research laboratories due to their small footprint. They are equipped with a turbo molecular pump (TMP) and the ultimate pressure of the deposition chamber reaches 8×10-6 Torr. Thermal evaporation deposition at this pressure creates a thin film with good quality and performance.
DTE deposition system with a single evaporative source holder contains a relatively smaller vacuum chamber (170 mm outer Dia chamber), which allows the pressure of the device to reach its minimum in a short time, while DTT with three separate source holders and large 300 mm Dia Borosilicate chamber allows longer run-times, multilayer deposition, performing co-evaporation processes and creating alloys.
The full range pressure gauge made by Leybold Company, with the ability to display pressure in the range of atmosphere pressure up to 10-9 Torr, is employed to continuously monitor the pressure of the deposition environment during the thermal evaporation process, which plays a significant role in the process of sample coverage and the quality of the thin film deposited by this method.
For more information about the DTE and DTT thermal evaporation systems, please visit Vac Coat website.
Some of Our Products
References
- https://akasharya.in/images/pdfs/MM731E1.pdf
- https://www.ndsu.edu/pubweb/~qifzhang/Tech_Sputter-01.pdf
- https://web.archive.org/web/20190427075315id_/https://cdn.intechopen.com/pdfs/52684.pdf
- Jilani, Asim, Mohamed Shaaban Abdel-Wahab, and Ahmed Hosny Hammad. “Advance deposition techniques for thin film and coating.” Modern Technologies for Creating the Thin-film Systems and Coatings 2, no. 3 (2017): 137-149.
- Rossnagel, S. M. (2003). Thin film deposition with physical vapor deposition and related technologies. Journal of Vacuum Science & Technology A: Vacuum, Surfaces, and Films, 21(5), S74-S87.
- https://www.inspirajournals.com/uploads/Issues/452078287.pdf
- https://en.wikipedia.org/wiki/Evaporation_(deposition)