What is the effect of chamber pressure on the grain size of Au and Pt sputtering deposited layers?
In sputtering deposition, many factors affect the grain size of the deposited layer. Target material, working pressure, and base pressure of the chamber can greatly influence the grain size. For a more detailed discussion on effect of base pressure on thin films grain size in magnetron sputtering deposition systems, you can see Effect of Base Pressure on Thin Film Grain Size in Sputtering.
How to achieve finer grain size in Pt deposition by magnetron sputtering?
Several parameters in a sputtering deposition process, like working chamber pressure and deposition power affect the layer grain size. Higher argon pressure (working gas pressure) (>50 mTorr) result in a lower density, porous and void structure; where higher sputtering power (larger current), rising temperature of the plasma and the substrate, results in larger particle size. Also, chamber ultimate pressure affects Pt grain size, which is discussed in the article titled as “Effect of base pressure on thin film grain size in magnetron sputtering” in our blog.
Sputtering parameters are influenced by the target used for the deposition. When utilizing a platinum (Pt) target, parameters like working chamber pressure and deposition power can vary the grain size of the layer. Higher argon pressure (>50 mTorr) result in lower density, porous and void structure, where density decreases from 20.8 g/cm3 at p=20 mTorr to 9 g/cm3 for p=200 mTorr. Lower density implies nucleation sites are spaced at a greater distance in the deposited layer, resulting in larger grain size.
Also, sputtering power used during deposition affects Pt np size; higher sputtering power (larger current) results in larger particle size. Since by increasing the power the temperature of the plasma and substrate rises, deposited layer contains larger particle size.
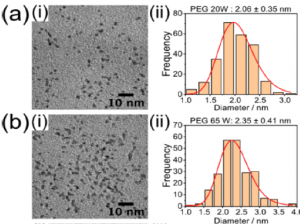
References
- ”Effect of pressure on dc planar magnetron sputtering of platinum”, May 2003 Journal of Vacuum Science & Technology A Vacuum Surfaces and Films 21(3):572-576
- Brown R, Lönn B, Pfeiffer R, Frederiksen H, Wickman B. Plasma-Induced Heating Effects on Platinum Nanoparticle Size During Sputter Deposition Synthesis in Polymer and Ionic Liquid Substrates. Langmuir. 2021 Jul 27;37(29):8821-8828. doi: 10.1021/acs.langmuir.1c01190.
Is it possible to deposit PTFE (Teflon) by RF Sputtering? What are normal deposition parameters?
Yes, PTFE (Teflon) can be sputter deposited by our RF magnetron sputtering systems. Parameters may differ from device to device, but in the literature the power is set less than 200 W, to avoid melting effects of Teflon targets. The deposition can be performed reaching 10-3 mbar (low vacuum) or 10-6 mbar (high vacuum) for the base pressure.
Why some sputtering targets need backing plate?
Several types of sputtering targets like ceramic, inorganic compound, most oxides, nitride and silicide targets are so fragile and show poor heat transfer, so they might crack during sputtering as a result of bearing thermal stress. To avoid this happen, it is recommended to bond such targets to an appropriate backing plate, whom characteristics might affect the deposition parameters.
Also, precious metal targets may need a backing plate, since thinner targets are normally preferred as it highly costs.
Is it possible to apply a bias voltage to the substrates to be coated?
Yes, one can bias the substrate by applying a DC voltage to it, which makes it possible to improve or modify the coating properties and the coating process for targets like ITO.
How can we measure thin film thickness?
Thin film thickness can be measures by various methods, depending on estimated range of thickness. For layers with thickness in the range of 1-2 nm, typical methods like AFM and ellipsometry are not recommended; since if not using highly smooth substrates like Si (100), substrate roughness influences thickness measurement. However; XPS and TEM characterizations are most proper choices. For thickness measurement during layer deposition, quartz crystal microbalance (QCM) technology is mainly used. Using Sauerbrey equation, which relates the mass change per unit area at the QCM electrode surface to the observed change in oscillation frequency of the crystal, one can measure the thickness of the deposited layer. (Read about thickness uniformity of thin films here)
How does pulsed laser deposition maintain the same composition between the source and deposited film?
Pulsed Laser Deposition can maintain the correct target composition since it is a pulsed process. In principle, the main mechanism can be explained as flash evaporation of 100% of a small part of the target in a few nano-seconds. So a small volume of the solid target is evaporated during the laser pulse entirely, no matter if different composite materials in the target have different vapor pressures. In contrast, vapor pressure normally determines the composition of the deposited film in an evaporation-based deposition method, where the deposited layer is rich in the materials with the highest vapor pressures.
What precautions can be taken during observation of non-conducting sample in FESEM?
To observe non-conducting (insulating) samples through Field Emission Scanning Electron Microscopy (FESEM), one have to coat the sample with a conducting metal like gold or platinum. Without coating, the resulting images of the sample will be distorted due to the collection of electron cloud near the sample surface, called ‘charging effect’. Also, coating is necessary in the case of imaging powder sample, as it protects the powder from evaporation under high applied electric field, which subsequently increases the lifetime of the electron gun of FESEM instrument.
What factors affect sputtering rates for coating with different targets?
The sputter deposition rate is related to the type of working gas and pressure, sputtering power applied to the target during deposition, including sputtering voltage and current, the temperature of the target, diameter of the target, the strength of the magnetic field, sputtering yield of the target and so on. For example for Cr, the sputtering rate could be 10nm/min, while for a gold target it can reach to 40nm/min. (You can use the Deposition Material Table for choosing the best method for your coating systems)
How could cracked sputtering targets affect film quality in RF magnetron sputtering?
In RF magnetron sputtering, if there are cavities or cracks on the sputtering target, it can be source of outgassing that may cause impurities in the deposited layer and degrade some layer properties, e.g. increase stress or create unwanted surface roughness and anisotropies. Cracks may also cause deposition of mesoscopic particles on the substrate which will deteriorate desired properties of the resulting thin film.
What is sputtering deposition?
Sputter deposition is a method of thin films deposition by sputtering material from a “target”. Sputtering is a term used to describe the mechanism in which atoms are ejected from the surface of a material when that surface is stuck by sufficiency energetic ions generated by low-pressure gas plasma, usually an argon plasma. The sputtering takes place at a much lower temperature than evaporation. Sputtered atoms ejected into the gas phase in vapor form are not in their thermodynamic equilibrium state and tend to condense on all surfaces in the vacuum chamber including the substrate.
Why are thin films important?
There are many useful applications for thin films. We desire to produce properties in a material that are often conflicting in nature if we use one homogeneous material. Semiconductor devices, for example, are fabricated on a thin layer deposited on a semiconductor substrate. The integrated electronic circuits depend on the confinement of electrical charges, which relies on the interfaces between different materials with different electronic properties.
There are also many occasions when the properties demanded for an engineering application involve features that are different for the surface than that are for the bulk. Depositing metal films and patterning them on the surface is relatively easy to secure electrical connection between semiconductor devices.
How does a sputtering system work?
Generally, in sputtering systems ions are generated and directed at a target, then ions sputter targets atoms. The ejected atoms are transported to the substrate and atoms condense and form a thin film. Below image shows the simple schematic of a sputtering system.
What are the advantages of sputtering systems compared to other thin films deposition methods?
Several methods are currently used for deposition of thin film layers. Physical vapor deposition methods (PVDs) are using low pressure, therefore, these methods reduce particulates and provide purer film qualities. The main categories of PVD processing are vacuum deposition (evaporation), sputter deposition, arc vapor deposition, and ion plating.
Sputtering is a versatile method, it gives us the capability to use scalable substrates, and it provides good stability and control over the deposition rate. Our sputtering systems are capable to place samples in different sizes and shapes on the substrate. High purity targets are available and interchangeable for sputtering systems; therefore, various types of materials, alloys and compounds can be sputtered and deposited. Although, the sputtering target provides a stable, long-lived vaporization source.
What are the applications of sputtering?
Sputtering has many well-known applications, such as the production of clean surfaces, deposition of metallic and insulating thin films, and analysis of surfaces and growth of active layers in devices. Thin film deposition allowed the development of many kinds of thin film electronic devices including thin film transistors (TFTs), surface acoustic devices, high-precision resistors, solar cells, magnetic and/or optical memory, liquid crystal display (LCD) and plasma display, and a variety of sensors and actuators.
Today, lots of thin films are widely used not only for information devices but also for energy and environmental systems like ecological buildings. Sputter deposition is widely used to deposit thin film metallization on the semiconductor material, coatings on architectural glass, and reflective coatings on compact discs (CDs), and for magnetic films, dry film lubricants, hard coatings (tools, engine parts), and decorative coatings. Below table gives typical thin film materials used for this applications.
What is DC sputtering?
Several sputtering systems are used for the deposition of thin films. Among these sputtering systems, the basic model is the DC diode sputtering system. The other sputtering systems are improved systems of DC diode sputtering.
What is RF Sputtering and how does it work?
In the RF Sputtering system, the thin films of the insulator are sputtered directly from the insulator target. In RF sputtering, it is easier to keep plasma going, it can operate at lower Ar pressures (1-15 mTorr). So there will be fewer gas collisions and therefore more line of sight deposition.
What is Reactive Sputtering?
Reactive sputtering is defined by the reaction between atoms sputtered from a metal target and reactive gas molecules diffused from a discharge gas on the substrate to produce compound thin films. The most essential process is the two-dimensional collision of metal atoms and reactive gas molecules on the substrate. When the reaction occurs on the substrate, the deposited film becomes a metal or oxide which is greatly affected by the deposition rate and the oxygen gas pressure. There are two different kinds of reactive sources: one is a gas source and the other is solid source.
For the gas sources reactive sputtering, the target is a nominally pure metal, alloy, or mixture of species. The gas source is a pure reactive gas or an inert-gas-reactive-gas mixture. The reactive gas comprises ingredient elements. The ingredients make the desired compound thin films. The reactive sputtering is realized by standard sputtering equipment; for instance, DC (or/none) magnetron sputtering or RF (or/none) magnetron sputtering. The reactive sputtering deposition is widely used in the industry. Reactive sputtering is a simple process for the deposition of the compound thin films.
Table 2: Reactive Gases Used in Reactive Sputtering, Some kinds of reactive gas are poisonous. Obtain expert advice on using these before the deposition.
Typically, a problem in dc reactive sputter deposition is preventing the “poisoning” of the sputtering target by the formation of a compound layer on its surface. Poisoning of a target surface greatly reduces the sputtering rate and efficiency. This problem is controlled by using an appropriate sputtering configuration (dual cathode, pulse power, etc.) at a high sputtering rate and controlling the availability of the reactive gas, such that there will be enough reactive species to react with the film surface to deposit the desired compound, but not so much that it will unduly poison the target surface.
What is Pulsed DC Sputtering?
During the reactive deposition process, regions on the target adjacent to the racetrack become coated up, or ‘poisoned’ with an insulating layer of the reactive product (e.g. Al2O3, TiO2, SiO2, etc.). The poisoned regions charge up until breakdown occurs in the form of an arc. Arc events cause severe problems during deposition. Each event disrupts the reactive process control system and can lead to the ejection of a droplet of target material, which may cause a defect in the growing film. Furthermore, the power supply will momentarily shut down to attempt to quench the arc, thereby reducing the deposition rate. Thus arcs are detrimental to the structure, properties, and composition of the coating and can lead to damage to the power supply.
The problems associated with DC reactive sputtering of dielectric materials were largely overcome through the introduction of the pulsed magnetron sputtering (PMS) process in the early 1990s. During pulsed sputtering, the target potential is periodically switched either to ground (unipolar mode) or to a positive potential (bipolar mode), at frequencies in the range 20-350 kHz. The most common mode of operation is the asymmetric bipolar one where, during the ‘pulse-off’ phase, the voltage is reversed to a magnitude equivalent to approximately 10% of the average voltage during the ‘pulse-on’ phase.
Figure 2: Pulsed DC can effectively reduce nodule formation on NiCr targets, pictured here, comparing Pulsed DC and straight DC power.

Figure 3: Micro-particles formation during DC sputtering process6.

I have a specific target material. How do I determine which type of power supply to use: an RF power supply or DC supply?
It’s certainly straightforward to determine if you need to use RF; you will need a simple ohm meter. Place both ohm meter leads anywhere on the target surface. If your meter reads infinity (for example, a pure alumina target will read infinity), your process requires RF power. On the other hand, if your ohm meter has a reading other than infinity, use an AC or DC power supply.
References
[1] Handbook of Gas Sensor Materials, Properties, Advantages and Shortcomings for Applications Volume 2: New Trends and Technologies, Springer New York Heidelberg Dordrecht London, 2014.
[2] Harsha: Principles of Physical Vapor Deposition of Thin Films Ch01, 2006
[3] Handbook of Physical Vapor Deposition (PVD) Processing, Donald M. Mattox, Second Edition-William Andrew (2010)
[4] Handbook of Sputter Deposition Technology. 2012 Elsevier
[5] Pulsed magnetron sputtering – process overview and Applications, P. J. KELLY, J. W. BRADLEY, JOURNAL OF OPTOELECTRONICS AND ADVANCED MATERIALS, Vol. 11, No. 9, September 2009, p. 1101 – 1107
[6] Pulsed DC Power for Magnetron Sputtering: Strategies for Maximizing Quality and Flexibility, D.R. Pelleymounter, D.J. Christie, and B.D. Fries, 2014 Society of Vacuum Coaters 505/856-7188 183, 57th Annual Technical Conference Proceedings, Chicago, IL May 3–8, 2014 ISSN 0737-5921
[7] Advanced Energy website