
An Overview of Pulsed Laser Deposition
Pulsed laser deposition is a physical vapor deposition technique in which a high-energy laser is focused on a target material in a vacuum chamber and converted to a plasma plume, which is deposited on a substrate (Figure 1). The deposition can be assisted by a flow of oxygen or other background gases, or occur under ultra-high vacuum conditions.
While the equipment needed to perform the deposition in this manner is roughly similar to other deposition methods (such as sputtering), the physical interaction between the laser beam and the target material and the formation of the thin film is very complex. Absorption of laser pulse energy by the target causes electron excitations, which can convert to thermal, chemical, and mechanical energy and evaporation of the target material.

The evaporated energetic particles, including atoms, molecules, ions, and electrons can form a plasma plume that will be deposited on the substrate.
The precise mechanism of the PLD process is complex, including the process of target material ablation by laser irradiation, the creation of plasma plumes with energetic ions, electrons, atoms, molecules, and charge-free particles, and the process of crystalline growth on the substrate.
Pulsed Laser Deposition (PLD) Process
The pulsed laser deposition process can be divided into four steps, each having a significant impact on the crystallinity, uniformity, and stoichiometry of the created thin film (Read more about Thickness Uniformity).
- Absorption of the laser on the target surface and interaction with the material, ablation, and plasma formation
- Plasma dynamics and laser-plume interactions
- Deposition of the material separated from the target on the substrate.
- Nucleation and growth of a thin film of the material on the substrate surface
Laser-Target Interaction
In the first phase, the laser beam is adsorbed on the target surface. Using sufficient high energy density and short pulse duration causes sudden heating up of all elements in the target surface to their evaporation temperature, where they are dissociated from the target by collisional, thermal and electronic excitation, and exfoliation and instantaneously ablated out with the same stoichiometry as the target.
Plasma Plume Formation
In the second stage, the ablated materials have a tendency to move towards the substrate according to the dynamic laws of gases and show the forward peaking phenomenon, creating a plasma plume.
Deposition on the Substrate
The high-energy species in the plasma plume impinge onto the substrate surface through the third stage. These energetic species sputter some of the atoms deposited on the substrate surface and a region is established where the incident flow and the sputtered atoms collide. Film growth happens directly next to this collision or thermalized region. This region condensates the energetic particles, so they can be deposited on the substrate (Figure 2).

Nucleation and Growth
The Forth stage, nucleation and growth of the crystalline thin films depends on many factors such as the density, energy, degree of ionization, the type of the condensing material, temperature, and the properties of the substrate. The nucleation process is influenced by the interfacial energies between the substrate, condensing material and the vapor. Deposition rate and the substrate temperature greatly affect the critical size of the nucleus. Large nuclei create isolate islands of the film on the substrates that grow and join together (Figure 3).

The crystalline film growth is determined by the surface mobility of the deposited atoms, which diffuse on the surface before fixing onto a stable position, highly dependent on the temperature of the substrate. Defect free crystal growth can occur at high temperatures, whereas deposition on a low temperature substrate may result in poor crystalline or even amorphous structure.
Which Laser is Used in PLD?
Each step in the PLD process is dependent on the target material, laser parameters like wavelength, fluence and pulse width, substrate, temperature, and deposition geometry. Wavelength of the lasers used in PLD studies ranges from the mid-infrared, like CO2 laser with a wavelength of 10.6 µm, through the near-infrared and visible, such as Nd-YAG laser with output wavelengths at 1064 nm and 532 nm, down into the ultraviolet. Most of the current PLD work employs excimer lasers operating at different UV wavelengths, e.g. 308 nm (XeCl), 248 nm (KrF), 193 nm (ArF), and 157 nm (F2).
The laser pulse should penetrate the surface of the target material to a specific penetration depth. The depth of penetration depends on the laser wavelength and refractive index of the target material at the laser wavelength. For most materials, this depth is about 10 nm. The strong electric field created by the laser beam causes the electrons to separate from the bulk. This process is performed in a pulse of 10 picoseconds or nanoseconds and occurs due to nonlinear processes such as multi-photon ionization.
Excimer versus ND: YAG laser
Excimer lasers offer the advantage of high-power output and stability. The Nd:YAG (neodymium-doped yttrium-aluminium-garnet) laser is simple in maintenance and provides a compact system compared to an excimer laser.
Excimer-based PLD applications are as follows:
- Fabrication of rare earth barium copper oxide films for multilayer high temperature superconductor tapes
- Creation of hydrogen-free DLC layers with great adhesion to a wide range of materials
- Enabling scandium-doped aluminum nitride thin films deposition for RF filters
- Producing crystalline thin films over large wafers (up to 300 mm) for use in micro-nano electronics
Laser characteristics influence the deposition parameters in several ways. Laser Pulse energy, repetition rate, fluence [Joule/cm2], and ionization degree of the ablated material affect the deposition flux (deposition rate), film quality, and the stoichiometry. The nucleation process and growth kinetics of the film also depend on these parameters; higher deposition flux leads to larger nucleation density.
PLD Targets
Since the most prominent feature of PLD method is saving the stoichiometry, various range of elemental and compound targets can be deposited through this technique. Al, Co, Ni, Boron, Zinc are typical metal elements used as targets for PLD, as well as compounds like YBa2Cu3O7 (YBCO), Yttrium Iron Garnet (Y3Fe5O12, YIG), Zinc Gallate (ZnGa2O4), Strontium Titanate SrTiO3, Barium Ferrite (BaFeO3), Bismuth Vanadate (BiVO4), etc.
PLD: Advantages and Disadvantages
PLD technique has several advantages that make it straightforward for thin film deposition, such as:
- Retaining the target stoichiometry in the deposited film
- Need to control only a few parameters related to the laser during the deposition, like laser energy density and pulse repetition rate
- Small targets required compared to other sputtering techniques
- Ability to produce multi-layered films of different materials by sequential ablation of various targets
- Controlling film thickness down to atomic monolayer by manipulating the number of pulses
- Lower substrate temperature needed compared to other deposition techniques
Main Disadvantages of Pulsed Laser Deposition Technique
However, several limitations in producing large area uniform thin films by pulsed laser deposition method have been identified that are listed below:
- Splashing or deposition of micrometer-sized particulates on the films because of sub-surface boiling, expulsion of the liquid layer, and exfoliation of the target
- Narrow angular distribution of the ablated species by the laser
Though these issues can be overcome by inserting a shadow mask to block off the large particulates, or rotating the target and substrate to produce larger uniform films, such shortcomings have hindered fully utilizing PLD in industry.
Pulsed Laser Deposition of Thin Films
Several techniques have been developed in PLD to obtain thin films with higher quality, grow thin films of targets made of polymers or biomaterials, deposition of multi-component targets and several multiple targets. Some of them are explained here.
PLD Methods
Scanning Multi-Component Pulsed Laser Deposition
In this method, a desired composition of various segments of the target containing different materials can be deposited by moving the scan line concerning the target geometry. This results in large area and uniform deposition of multicomponent coatings (Figure 4).
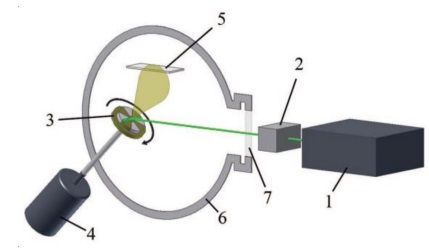
Combined PLD and Magnetron Sputtering
By combining PLD and magnetron sputtering (MS), the magnetron discharge can be maintained at lower pressures compared to a typical MS system, which results in higher deposition rates and direct deposition of clusters, and neutral atomic species by PLD (Figure 5).

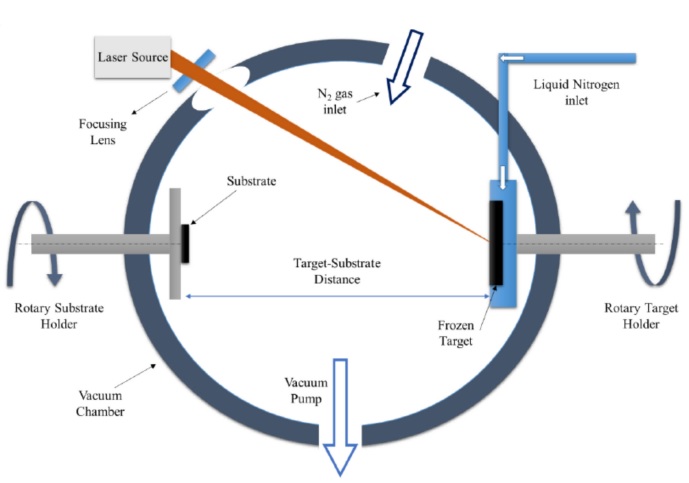
Matrix Assisted Pulsed Laser Evaporation (MAPLE)
It is a useful method to deposit frozen targets of inorganics, polymers, and biomaterials dissolved in a volatile solvent, which adsorbs high energy laser beam and prevents damage to the material molecules. Target molecules are heated up through collision with solvent molecules and convert to vapor phase, where solvent vapor is easily pumped out due to their lower adhesion coefficient (Figure 6).
Multi-Beam PLD
This PLD method is mainly used to deposit a thin film from multi-targets of different materials by mixing more than one plasma plume during thin film deposition (Figure 7).

Off-Axis PLD
In off-axis PLD technique, the substrate is placed parallel to the plasma plume, which results in the deposition of thinner and more uniform films on the substrate compared to the on-axis substrate (Figure 8).

Pulsed Laser Deposition Applications
Pulsed laser deposition has attracted widespread interest since the successful growth of high-temperature superconducting films in 1987. This technique has been employed to fabricate various materials, including:
- Epitaxy crystalline thin films
- Nitride films
- Metallic multilayers
- Ceramic oxides
- Superlattices
- Nanotubes
- Nanopowders
- And quantum dots
Because of the high heating rate and lower substrate temperature in PLD compared to other deposition methods, semiconductors, and the underlying integrated circuits can be deposited through PLD.
Vac Coat PLD
The Vac Coat Co. PLD-T is a high vacuum thin film deposition system. This device is equipped with the target manipulator system with adjustable rotation speed. This pulsed laser deposition (PLD) system is capable of producing thin films of uniform composition and thickness in all substrate areas. It also has a vacuum thermal evaporation with three heat evaporation sources to perform thermal evaporation coating.
PLD-T is equipped with quartz crystal monitoring system for real time thickness measurement (1 nm precision), as well as a plasma cleaning option, rotatory sample holder and electronic shutter, that can be controlled by an intuitive touch screen to control the coating process and rapid data input with a updatable user friendly software. For more information visit the site of Vac Coat Company.
Other Deposition Systems
References
- Ogugua, S. N., Ntwaeaborwa, O. M., & Swart, H. C. (2020). Latest Development on Pulsed Laser Deposited Thin Films for Advanced Luminescence Applications. Coatings, 10(11), 1078. doi:10.3390/coatings10111078
- Benelmekki, M., & Erbe, A. (2019). Nanostructured thin films–background, preparation and relation to the technological revolution of the 21st century. Nanostructured Thin Films, 1–34. doi:10.1016/b978-0-08-102572-7.00001-5
- https://repositorio.ul.pt/bitstream/10451/1635/12/19492_ulsd_re481_CHAPTER_3.pdf
- P.R. Willmott and J.R. Huber, “Pulsed laser vaporization and deposition”, Rev. Mod. Phys. 72 (2000) 315-328
- A. Giardini, V. Marotta, A. Morone, S. Orlando and G.P. Parisi, “Thin films deposition in RF generated plasma by reactive pulsed laser ablation”, Appl. Surf. Sci. 197 (2002) 338-342.
- Pulsed Laser Deposition of Thin Films, edited by Douglas B. Chrisey and Graham K. Hubler, John Wiley & Sons, 1994 ISBN 0-471-59218-8
- Vaziri, M R R (2010). “Microscopic description of the thermalization process during pulsed laser deposition of aluminium in the presence of argon background gas”. Journal of Physics D: Applied Physics. 43 (42): 425205.
- Ohnishi, Tsuyoshi; Shibuya, Keisuke; Yamamoto, Takahisa; Lippmaa, Mikk (2008). “Defects and transport in complex oxide thin films”. Journal of Applied Physics. 103 (10): 103703–103703–6. Bibcode:2008JAP…103j3703O
- May-Smith, T. C.; Muir, A. C.; Darby, M. S. B.; Eason, R. W. (2008-04-10). “Design and performance of a ZnSe tetra-prism for homogeneous substrate heating using a CO2 laser for pulsed laser deposition experiments, doi:10.1364/AO.47.001767
- https://andor.oxinst.com/learning/view/article/pulsed-laser-deposition
- Y. Zhang, H. Gu, and S. Iijima, Appl. Phys. Lett. 73, 3827 (1998)
- D.B. Geohegan, A.A. Puretzky, and D.L. Rader, Appl. Phys. Lett. 74, 3788 (1999)
- T.J. Goodwin, V.L. Leppert, S.H. Risbud, I.M. Kennedy, and H.W.H. Lee, Appl. Phys. Lett. 10, 3122 (1997)
- http://groups.ist.utl.pt/rschwarz/rschwarzgroup_files/PLD_files/PLD4.htm
- https://en.wikipedia.org/wiki/Pulsed_laser_deposition
- https://www.trieste.nffa.eu/techniques/growth/pld
Which laser is preferable for pulsed laser deposition?
In pulsed laser deposition (PLD) method, a short-wavelength laser, such as KrF excimer laser with a wavelength of λ=248 nm, is focused onto the target to create a plasma plume of the material. You can see your PLD System here.
Which stage has the key role in determination of the thin film quality in PLD?
The third stage, in which the decomposition of the ablation materials onto the substrate happens, highly affects the thin film quality.
How viable is PLD in replacing sputtering process for Sc-doped AlN deposition in high volume manufacturing?
Generally, PLD technique is a method for deposition on small surfaces (with max. 10 cm dia. ) and is not certified for creation of uniform coatings on large substrates as used for industrial purposes. However, you can find more information in the scientific literature on the subject.