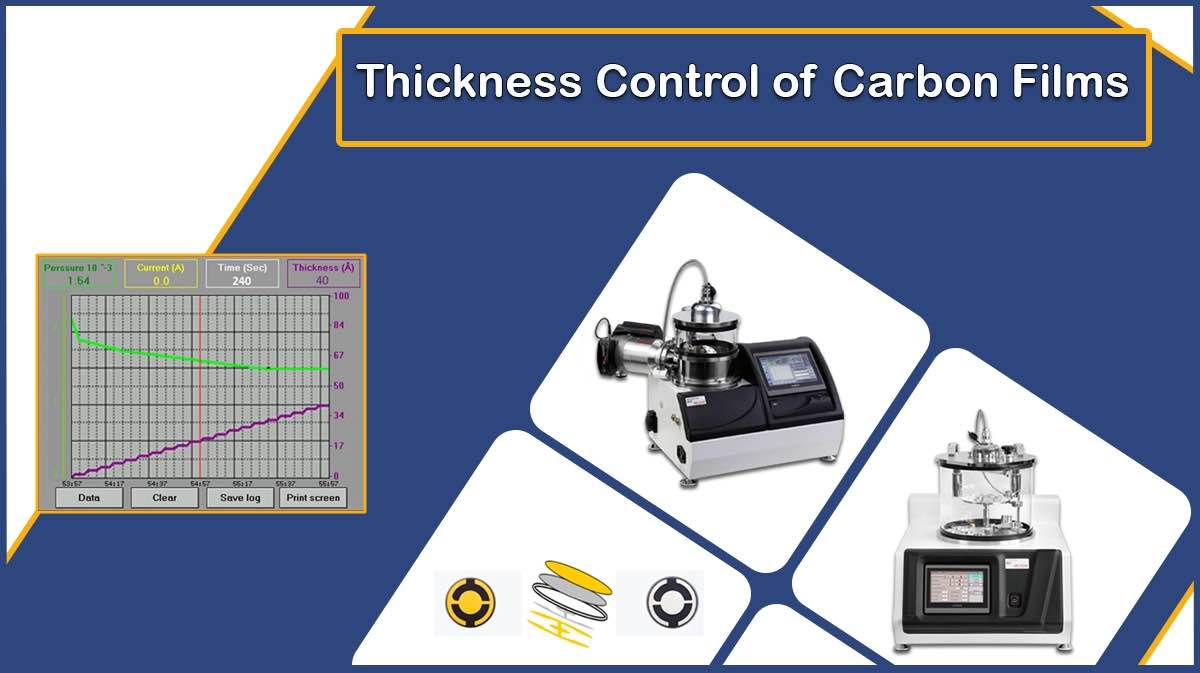
Precise Thickness Control of Carbon Film in Vacuum Carbon Coaters
Control of carbon film thickness deposited on the samples to be analyzed by electron microscopy (SEM, TEM, FE-SEM, and etc.) or Energy-dispersive X-ray spectroscopy (EDX) should be accurate to obtain the best result. The QCM monitoring of the thickness of carbon thin film deposition by resistive evaporation of carbon sources (Rod or Fiber) happens at high temperatures that may cause sensor heating and failure.
Pulsed Carbon Fiber Evaporation Process
Pulsed carbon fiber evaporation process can be used to overcome the thickness measurement failure during deposition and have a precise, uniform carbon coating. The pulsed carbon evaporation fiber is available in Vac Coat carbon coaters as a manual or automatic coating process.
In this technique, the low duration high-current pulses (Nearly 2 seconds) prevents heating up the sensor.


Ramped Carbon Rod Evaporation Process
In the case of carbon rods, higher DC current should be applied to evaporate them, which can enhance the thickness sensor temperature and cause fake thickness signals. The ramped increase in the current passing the carbon rods can control the amount of heat generation and better QCM sensor stability during thickness measurement, as well as more uniform carbon layer deposition. Vac Coat carbon coaters with rod evaporation head (Optional) provide automatic ramped carbon rod evaporation process to ensure uniform and reliable carbon rod evaporation process.
Vacuum Carbon Coating Systems Applications
Low vacuum and high vacuum carbon coaters have a wide range of applications, including:
- Electrode deposition
- Preparation of electron microscope samples by coating a conductive thin film
- Creating TEM grid supporting film
- Deposition of carbon replicas
Precise Control of the TEM Grid Supporting Carbon Film Thickness
In imaging samples with TEM, it is necessary to cover the TEM grids with a supporting thin film of carbon, in which case the reproducibility of the carbon film thickness and also the quality of the deposited thin film play an important role in the image quality. Therefore, it is necessary to use a system for carbon coating, that is able to regenerate deposition of high-quality carbon layers with precise real-time measurement of the thickness of carbon thin film.
Film Thickness Monitoring
The common film thickness monitoring method in vacuum coating systems involves using Quartz Crystal Microbalance (QCM) sensors. A QCM sensor is a piezoelectric crystal whose resonant frequency changes with its mass, which can be related to the thickness of the layer deposited on it.

QCMs show thermal dissipation at elevated temperatures, depending on the crystal cut and the type of electrode material used in their structure. Whereas AT-cut QCMs with gold electrodes are stable at room temperature, the ones with silver electrodes can withstand thermal shocks that happen in carbon evaporation processes.
Vac Coat Vacuum Carbon Coaters
Vacuum carbon coating systems, Desk Carbon Coater – DCR, Turbo-Pumped Carbon Coater – DCT, Desk Sputter and Carbon Coater – DSCR, and Turbo Pumped Sputter & Carbo Coater – DSCT models, made by Vac Coat Ltd. using pulsed power supply sources provides the ability to control carbon film thickness. The carbon coaters are also equipped with three carbon fibers and have the ability to detect burning and switching onto another. These systems allow the users to adjust the number of pulses and the current.
All Vac Coat carbon coaters can be equipped with carbon rod evaporation head, enabling programmable ramped carbon rod evaporation process that allows precise monitoring of the thickness of carbon thin films during deposition process.
The DCT-300 large chamber high vacuum carbon coater and DSCT-300 dual sputter and carbon coater are Vac Coat new coating systems that allow thin film deposition on larger substrates, up to 15 cm in diameter. Also, these vacuum carbon coating systems are equipped with accurate and efficient thickness gauges that accurately display the thickness of carbon thin film with an accuracy of 1 nm during the deposition process and the deposited carbon film thickness with time is observable as curve or data on the main screen.