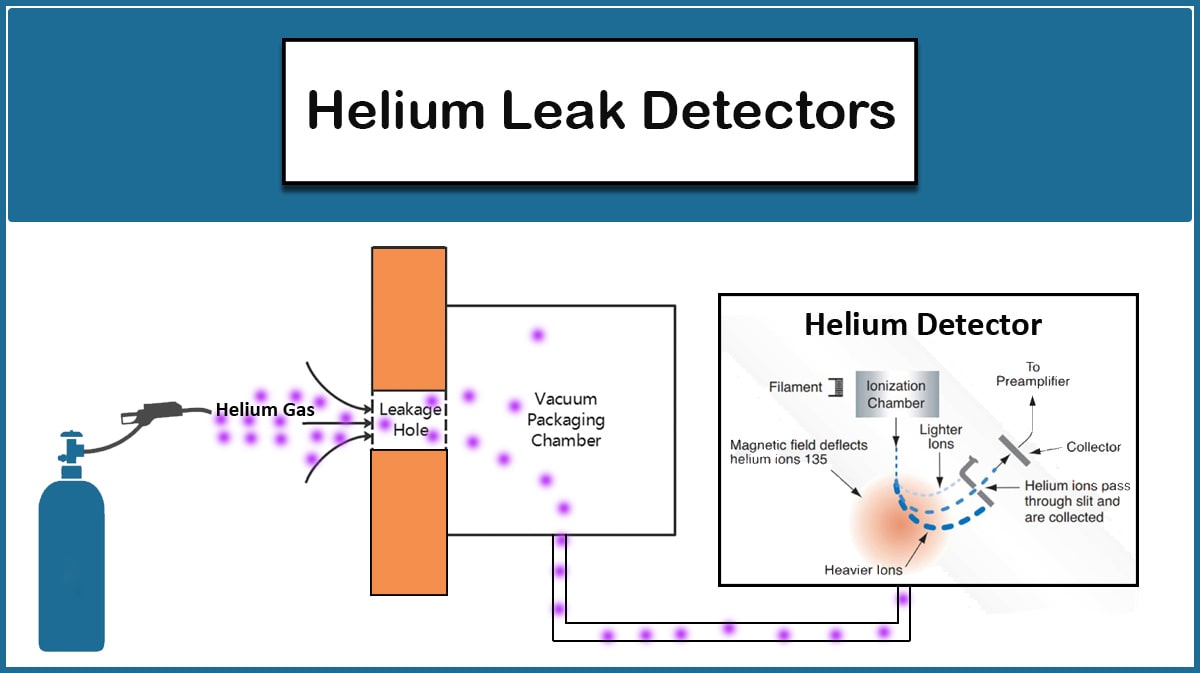
Mass Spectrometer Leak Detector (MSLD)
Helium Leak Detector (HLD), also known as the Mass Spectrometer Leak Detector (MSLD), is an instrument commonly used to find the location of the leakage and measure the rate of it in a system. Among several methods of leak detection, helium leak test is the most accurate one.
What is A Vacuum Chamber Leak?
Ideally, the vacuum chamber should retain the vacuum after the pumps have been turned off. But in real systems, over time, system pressure increases. This increase in pressure can be due to the penetration of wall molecules (Outgassing) or due to leakage and penetration of molecules from outside into the system.
Two Types of Leaks
Accordingly, there are two types of leaks, residual gas leaks and virtual leaks. A residual gas leak is a real leak due to incomplete sealing, or the existence of holes or micro-cracks in the system. A virtual leak is caused by the outgassing of chemicals trapped or adhered to the interior part of a system.
In fact, no vacuum system can completely be without leaks. What is important is that the leakage should be small enough that the final pressure and gas balance in the chamber does not disturb the vacuum. Also, determining the allowable limit of the leak for each vacuum system is essential. Therefore, leak detection is an important step in creating a vacuum system and guaranteeing the desired final pressure. For more information, please visit the blog article “The Importance of Vacuum Leakage Detection”.
Why Use Helium in Vacuum Leak Detection?
Helium as a non-toxic, inert, non-flammable, and non-explosive gas, is the most suitable choice for leak detection. It exists in our environment with a concentration of about 5 ppm. It is relatively inexpensive and is available in cylinders of different sizes. Because of its small atomic size, helium gas can easily pass through leakage pores. It was initially developed in the Manhattan Project during World War II to find extremely small leaks in the gas diffusion process of uranium enrichment plants.
Helium Leak Detection (HLD) Methods
There are various methods for vacuum leak detection using helium gas, which can be used based on the operating conditions of the vacuum system. In general, determining the location of the leak and the amount of leakage are two important issues that are followed in all procedures. Two main methods in helium leak detectors are vacuum tests (Outside-in) and pressure tests (Inside-out).
Vacuum Test Method
i. Helium Spray Method
In the vacuum test method, first the system should be vacuumed by an external vacuum pump or pump mounted on the system. The helium is then sprayed in places suspected of leakage. If there is a leak, helium molecules penetrate into the chamber and the helium leak detector sensor which is inserted into the vacuum chamber detects them. This will determine the location of the leak (Figure 1).
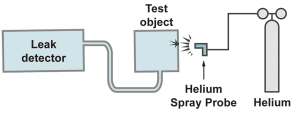
ii. Bell Jar Method
To determine the overall leakage value of the system, the test object is placed in a chamber under a special helium gas pressure. In this case, all leak sites are detected by a helium mass spectrometer (Figure 2).
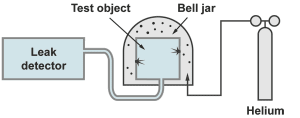
Pressure Test Method
i. Sniffer Probe Method
In the pressure test method, the test object is first filled with helium gas or a mixture of helium gas and air. Leak-suspected sites are then scanned by the helium leak detector. If there is a helium gas, the leak detector starts to sound the alarm, and so the location of the leak is determined (Figure 3).
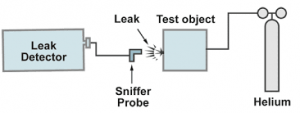
ii. Bombing Method
To determine the overall leakage rate of the system, the test object is filled with helium gas and placed inside a pumped chamber with a leak detector. The amount of helium gas passing to the vacuum pump is measured by a helium leak detector; thus, the total amount of system leakage is determined (Figure 4).
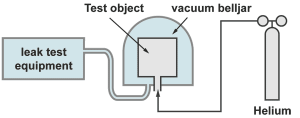
Suction Cup Method
This method is very useful for test objects that cannot be put inside another vacuum chamber or cannot be totally evacuated as a consequence of product condition (For example in case of large containers) or the manufacturing process. The suction cup method can be applied in various cases like:
- Checking the manufacturing process of large vacuum chambers
- Finding the local leakages
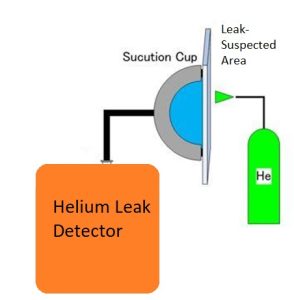
How Does A Helium Leak Detector Work?
The principle performance of a leak test unit is based on the ionization of the helium gas by an electron beam produced by a filament in the analysis tube. The ions are accelerated by applying a voltage of about 400 to 1200 V, and then pass a slit and move through the magnetic field generated by the analyzer. The radius of deviation of the ions varies depending on their mass-to-charge ratio in a magnetic field. So, the ions under the magnetic field are separated by their mass-to-charge ratio and those with larger mass have a greater radius of deviation.
Since the circular trajectories of the ions depend on their mass, the collector can catch only the helium ions and detect helium. Then the flow of ions collected by a detector is converted into electrical current and displayed on a screen. The measured electrical current is monitored by a leakage display unit on a screen. The measured electrical current is directly proportional to the concentration of helium and therefore equals the amount of leakage. For very low leaks, very small currents of about 10-15 amps is detected which is equivalent to a sensitivity of 10-12 mbar.L/sec.
It should be noted that the path of the ions in the mass spectrometer from the ion source to the collector is approximately 15 cm. Since the ions must travel this path without colliding with the gas molecules, the mean free path should be at least 60 cm (In the high vacuum range). Therefore, the mass spectrometer operates in high vacuum conditions.
Helium leak detectors usually include the following parts:
- Helium Mass Spectrometer Leak Detector (MSLD)
- Control systems and valves that control various stages of testing including measurement, vacuuming, testing, and venting
- High vacuum and backing vacuum pumps, such as turbomolecular and rotary, and pumps
- Vacuum pressure gauge
- A device that connects the test unit to the leak detector

Challenges Using Helium Leak Detection Method
There are several challenges accompanying detection of small leaks utilizing helium that should be noted. Ambient or entrapped helium may affect the accuracy of leak detection and measurement with extremely sensitive helium leak detectors. Leak detector unit can also amplify leakage problem since they are not leak-proof, so a helium-clean environment is essential for accurate leak detection. Also, external factors and helium permeation through exhaust and venting ports, and O-rings can negatively influence the results in detection of very small leaks.
Leak Detection of Vacuum Coating Systems
Thin film deposition by PVD (Physical Vapor Deposition) methods requires a vacuum environment to fabricate a clean coating on the specimen. Vac Coat Ltd. uses helium leak detector for the detection of any leaks in vacuum coating systems made by this company, including sputter coaters, carbon coaters, thermal evaporators, and pulsed laser deposition systems.
Some of Vac Coat Products
Resources
- Ahmadi, Afsaneh; Moenie, Mahdi; Kowsari, Mohammadreza, Leak detection of vacuum systems using helium leak detector.
- N. Hilleret. LEAK DETECTION. Geneva, Switzerland: CERN. At the origin of the helium leak detection method was the ”Manhattan Project” and the unprecedented leak-tightness requirements needed by the uranium enrichment plants. The required sensitivity needed for the leak checking led to the choice of a mass spectrometer designed by Dr. A.O.C. Nier tuned on the helium mass. Because of its industrial use, the material choice (originally glass) turned out to be unbearably fragile and after many complaints by the users, a new metallic version was developed and constructed. The sensitivity of the apparatus was in 1946 ~10−7 Pa·m3·s−1 and it increased to ~10−10 Pa·m3·s−1 by 1970. Nowadays the quoted sensitivity of the most sensitive detectors is ~10−13 Pa·m3·s−1, a factor 106 gain within 50 years”
- Robert Brockmann. “UST method”. researchgate
- https://www.iitk.ac.in/ibc/HLDr.pdf
- https://www.fukuda-jp.com/en/leak/
- https://odishaexpo.com/global-helium-leak-sensor-market-2020-growth-analysis/
- https://www.leybold.com/en/knowledge/vacuum-fundamentals/leak-detection/using-helium-for-industrial-and-integral-leak-tests
- https://www.leybold.com/en/knowledge/blog/finding-vacuum-leaks-using-helium
- https://showcase.ulvac.co.jp/en/how-to/product-knowledge07/testmethod.html
- Medhe, Sharad. “Mass spectrometry: detectors review.” Chem Biomol Eng 3.4 (2018): 51-58.
I am text block. Click edit button to change this text. Lorem ipsum dolor sit amet, consectetur adipiscing elit. Ut elit tellus, luctus nec ullamcorper mattis, pulvinar dapibus leo.
Looking forward to your next post. Keep up the good work!