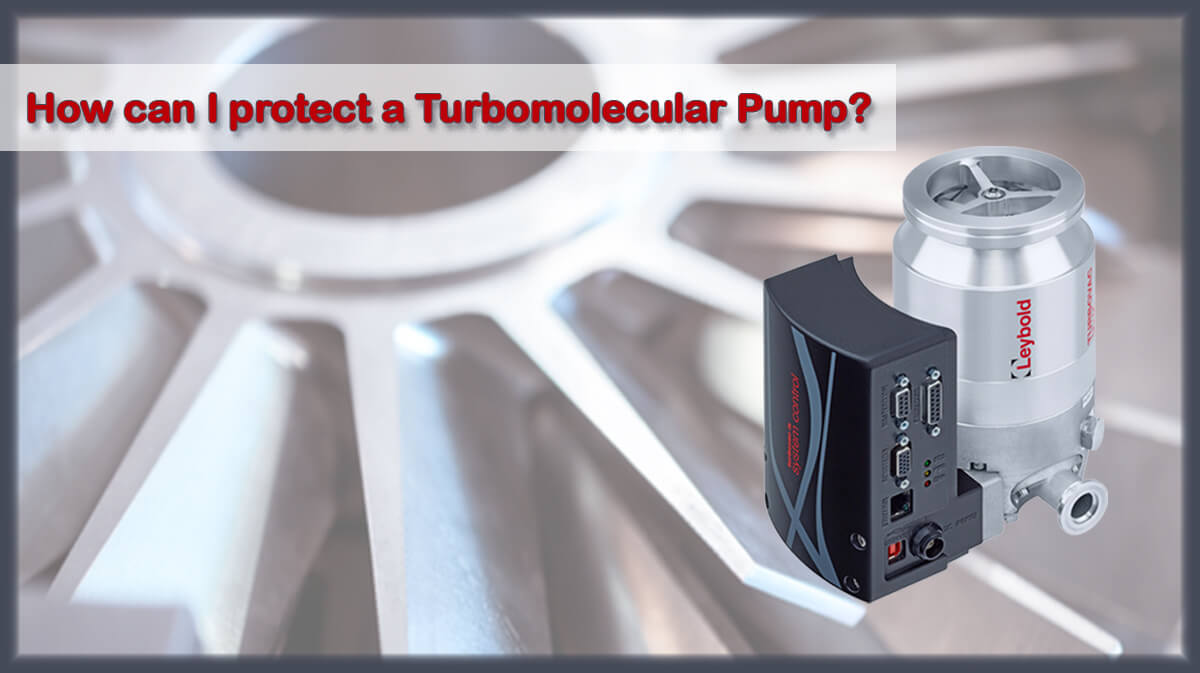
How can I protect a Turbomolecular Pump?
There is a wide range of mechanical pumping techniques that perform medium vacuum and provide long-time trustworthiness. However, to create High Vacuums (HV) and Ultra-High Vacuum (UHV) for advanced scientific and technological fields which are required in thin-film fabrication devices such as Thermal Evaporation Coating Devices, Sputtering Coaters, Carbon Coaters, Pulsed Laser Deposition (PLD) and the manufacturing processes of layer deposition require for solar cells, semiconductors, optical filters, magnetic sensors, and scanning electron microscope (SEM) sample preparation a turbomolecular vacuum pump with the most highly engineered design is necessary.
There are not any contact seals or rubbers in turbomolecular pumps (TMP) such as oil. As a rule, the rotor blades are spinning a few tenths of a millimeter from the envelope of the pump and the rotor shaft is a few tenths of a millimeter from the stator blades. These gaps require for the running pump; however, they make a condition that a small fraction of the gas to backstream (flow backward) over the pump. This is one reason that turbomolecular vacuum pumps must have a mechanical backing pump supplying a rough vacuum pressure on the exhaust port. In other words, the turbomolecular pump must be “backed” by a roughing pump (mostly a Rotary Vacuum Pump).
Since the failure of turbomolecular pump in thin film deposition systems is directly linked to the shutdown of the whole system and causes a large loss, the TMPs should examine and the necessary maintenance items should confirm to realize stable equipment operation.
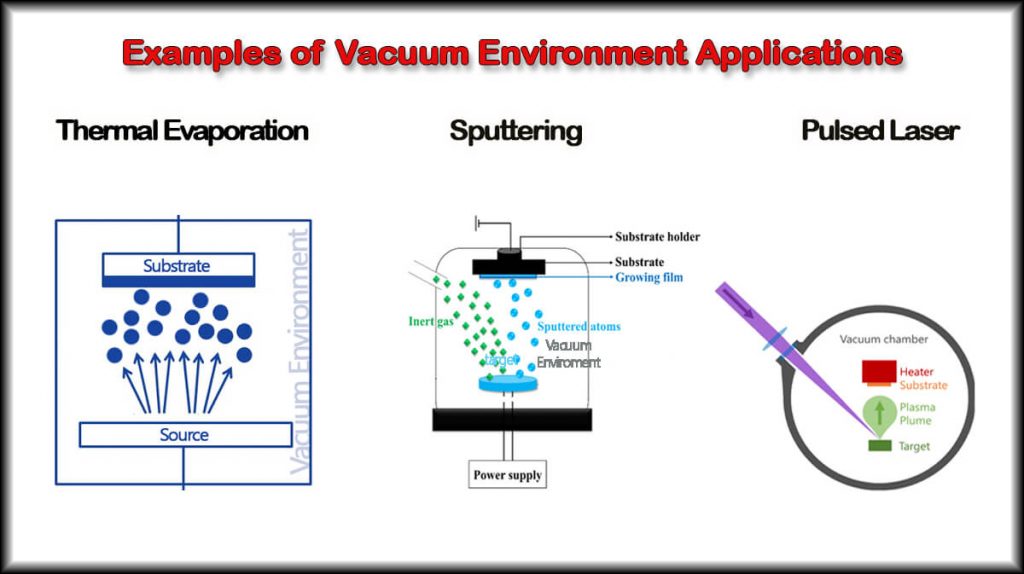
Turbomolecular vacuum pumps operate using a very fast spinning rotor (commonly between 22,000 and 95,000 RPM). Their usual operating pressures are in the high vacuum to ultra-high vacuum extent between 10-3 and 10-11 mbar. Consequently, the pump becomes overheated or in a severe situation, it crashes because the fast-moving items get in touch with the stable blades. Pump engineers suggested some conditions that must be considered for the right operation and long-lasting of a turbomolecular pump.
- Firstly, it is necessary for the vacuum pump, chamber, and pipes to be clean and leak-tight. There are several methods for measuring vacuum leakage, the most important of them is the use of a Helium Leak Detector.
2. In addition, the foreline pressure is also essential. Foreline is the part of piping between the turbo molecular pump and the mechanical backing pump (a rotary vane). Pressure measurement in the foreline is recommended to make sure that there is enough vacuum so that the turbo is correctly backed. A standard backing pump pressure is on the order of 10-2 or 10-3 Torr for rotary vacuum pumps and 1 Torr for the vacuum diaphragm pumps, pressures higher than these in the foreline will have the same issue as a heavy leak or other contribution to the way gas load, including pollution that causes the pump to overheat and shut down.
3. There is also a cooling unit with a turbomolecular pump (air-cooled or water-cooled) and this unit must be running efficiently to avoid overheating. If the system is air-cooled such as turbomolecular pumps in Vac coat Systems, the fans must be kept in working, and the ambient air temperature around the turbo cools enough to facilitate heat transfer. If it is water-cooled, the water must move at a flow rate and temperature proper to maintain a normal operating temperature.
4. A further sign of a pump failure is its sound. When a pump is in perfect condition, it should be nearly soundless, vibration-free, and calm such that you need to refer to the monitor or the system pressure gauges to know whether it is operating or not. The noise from the rotary vane backing pump should be the main sound from the system. If the pump is making a high-pitched sound, it may be that the turbo pump is crashing. If the sound or noise increases every second, this is another sign of crashing, and the pump must switch off immediately.
5. If the temperature growth in the pump is very fast, for example, a flight from 24oC to +55oC in a couple of minutes, there is severe rotational resistance. Possible causes could be contamination growth from condensed process materials on the rotor blades. At this stage, the pump should be taken out from the system for further examination. Once removed, be careful, because the turbine blades can be very sharp, give them a spin. If all is well they should spin freely for +15 seconds or more.
6. The entry of any liquid or particles into the pump, especially when the pump is running and rotating at high speed, will damage the blades and the pump will stop working. All the vacuum coating systems produced by VacCoat Co. are designed in such a way that it is not possible to deposit any layers on the blades of turbomolecular vacuum pump. Another hazard that threatens turbo pumps is the entrance of foreign objects and massive particles on the high-speed spin-moving blades of the turbo pump. In all coating devices manufactured by VacCoat Ltd. in the gates of turbomolecular pumps, some series of grids with very small pores have been used to prevent particles from entering the pump.
7. It must be noted that when the turbomolecular vacuum pump runs and rotates at its maximum speed, it should not be moved.
8. Experts recommend keeping the pump under vacuum when your coating processes are finished. This prevents dust and humidity from getting on the pump chamber and damaging it.
9. Another important aspect about how taking care of turbomolecular pumps is when these pumps are rotating, the vacuum should not be broken in any way because this will damage the pump rotors. So, to break the vacuum, be patient until its rotation comes to a complete stop.